BECT
Civil/Environmental
- May 11, 2020
- 22
Hello,
We were in the process of coring 64mm dia. hole for Williams anchors. Our core bit stuck when it was 57" into the concrete. I am planning to do additional 75mm hole on top of it and take this core bit out and then grout it back . Once the grout is set , I will drill hole again 64mm hole. Has anybody encountered similar problem.
Another idea is to put pipe in the bit and weld all around and then pull it with jack.
see attached picture. Let me know your thoughts
Thanks
We were in the process of coring 64mm dia. hole for Williams anchors. Our core bit stuck when it was 57" into the concrete. I am planning to do additional 75mm hole on top of it and take this core bit out and then grout it back . Once the grout is set , I will drill hole again 64mm hole. Has anybody encountered similar problem.
Another idea is to put pipe in the bit and weld all around and then pull it with jack.
see attached picture. Let me know your thoughts
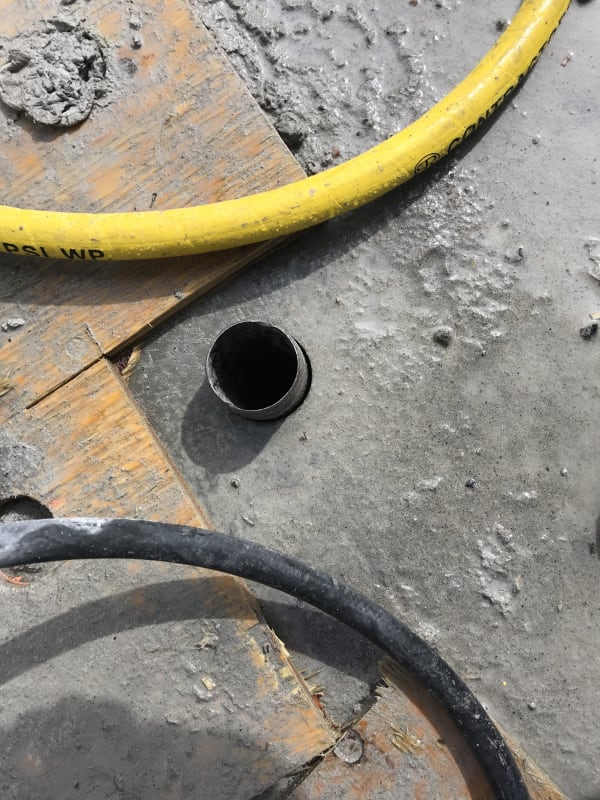
Thanks