Nerbie97
Civil/Environmental
- Apr 16, 2022
- 9
Hi all,
A friend is building a new house, and has approached me to design his suspended slab which will support a two-gar garage above. The area below will be storage space. The plan dimensions are roughly 5500mm x 6000mm and he does not want to have any columns interrupting his space below. We are in Eastern Canada.
The garage is surrounded by foundation walls which sit 12" above the final top of slab elevation. Initially, I had done a quick check assuming a concrete slab - with & without concrete beams - and we found that it'd be too expensive to meet deflection criteria. I explored some options & read the few posts on elevated garage slabs here, evaluated some other options with the client & currently we are going with a slab on steel deck. The 6000mm span will essentially be cut in 3, for three (roughly even) spans of <2000mm. Instead of bearing the slab on the foundation wall, I'm opting to place two beams on the extremities as end-bearing beams & slightly prolong the slab to finally sit on an angle anchored in to the wall. I figure this way, only a check for the shear capacity of the angle is in order for the foundation walls.
I understand the challenges with steel construction below a garage - the client understands this very well as well and an effort will be made to prevent water from seeping in through the perimeter joints. Galvanized steel components are also in the question.
My principal concerns at the moment are water considerations which is why I am having doubts about the choice of steel deck. Would specifying galvanized steel & detailing a water-tight expansion/flexible joint around the perimeter of the slab be sufficient to ensure the performance of this structure? In a previous post, a user completely ignored the decks contribution (over the long-term) as they assumed salt would eat up the deck below over time.
Furthermore, how would one design for drainage in an elevated slab? I wanted to put a drainage canal at the front of the garage (right behind the door) and give the whole garage a 3" slope towards it. But, I am worried about a car's wheel load over the canal. How would you support the canal from below?
Also, judging based on past threads here, many have used this option (in various jurisdictions) - I can't seem to find any resources which indicate if this construction is permitted with regard to fire safety considerations.
Attached are two preliminary details I have (very roughly) drawn.
I would appreciate any and all constructive comments. Thank you.
A friend is building a new house, and has approached me to design his suspended slab which will support a two-gar garage above. The area below will be storage space. The plan dimensions are roughly 5500mm x 6000mm and he does not want to have any columns interrupting his space below. We are in Eastern Canada.
The garage is surrounded by foundation walls which sit 12" above the final top of slab elevation. Initially, I had done a quick check assuming a concrete slab - with & without concrete beams - and we found that it'd be too expensive to meet deflection criteria. I explored some options & read the few posts on elevated garage slabs here, evaluated some other options with the client & currently we are going with a slab on steel deck. The 6000mm span will essentially be cut in 3, for three (roughly even) spans of <2000mm. Instead of bearing the slab on the foundation wall, I'm opting to place two beams on the extremities as end-bearing beams & slightly prolong the slab to finally sit on an angle anchored in to the wall. I figure this way, only a check for the shear capacity of the angle is in order for the foundation walls.
I understand the challenges with steel construction below a garage - the client understands this very well as well and an effort will be made to prevent water from seeping in through the perimeter joints. Galvanized steel components are also in the question.
My principal concerns at the moment are water considerations which is why I am having doubts about the choice of steel deck. Would specifying galvanized steel & detailing a water-tight expansion/flexible joint around the perimeter of the slab be sufficient to ensure the performance of this structure? In a previous post, a user completely ignored the decks contribution (over the long-term) as they assumed salt would eat up the deck below over time.
Furthermore, how would one design for drainage in an elevated slab? I wanted to put a drainage canal at the front of the garage (right behind the door) and give the whole garage a 3" slope towards it. But, I am worried about a car's wheel load over the canal. How would you support the canal from below?
Also, judging based on past threads here, many have used this option (in various jurisdictions) - I can't seem to find any resources which indicate if this construction is permitted with regard to fire safety considerations.
Attached are two preliminary details I have (very roughly) drawn.
I would appreciate any and all constructive comments. Thank you.
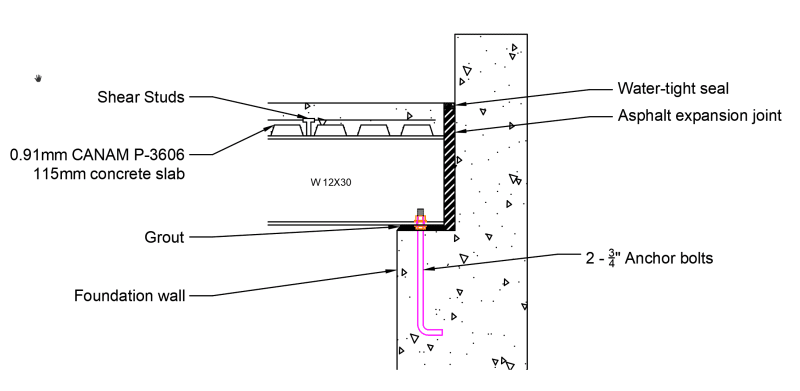
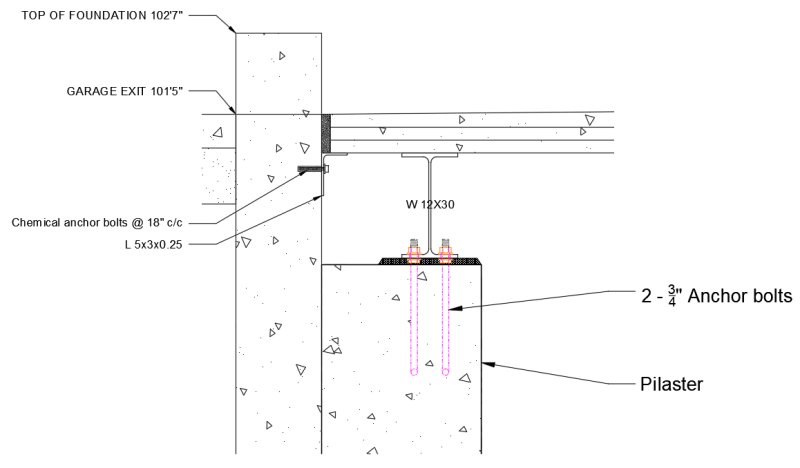