Hypothetical wall section attached.....
Has as anyone ever dealt with a tall single story wood framed building, where the wall height is tall enough where full height studs are not feasible. This results in a bottom portion of the wall and a top portion of wall, which creates a "hinge" in the wall. I am curious if anyone has ever encountered this and how this is dealt with. There has to be wood framed buildings out there with this type of scenario.
I am looking for y'alls thoughts, discuss, experience. Where I am perplexed is wind load on the face of the wall, obviously resulting in shear and moment which needs to transfer across this "hinge". The shear transfer probably isn't a concern, transferring moment across this gets interesting. Do you put metal strapping each side of the studs designed for the decoupling forces? Do you consider composite action with the exterior sheathing and then require interior sheathing also for composite action?
Yes, kickers up to the roof structure would be the easiest, but this isn't an option. I look forward to everyone discussion.
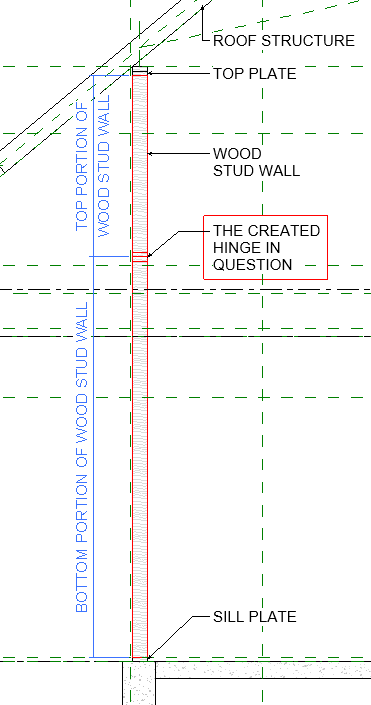
Has as anyone ever dealt with a tall single story wood framed building, where the wall height is tall enough where full height studs are not feasible. This results in a bottom portion of the wall and a top portion of wall, which creates a "hinge" in the wall. I am curious if anyone has ever encountered this and how this is dealt with. There has to be wood framed buildings out there with this type of scenario.
I am looking for y'alls thoughts, discuss, experience. Where I am perplexed is wind load on the face of the wall, obviously resulting in shear and moment which needs to transfer across this "hinge". The shear transfer probably isn't a concern, transferring moment across this gets interesting. Do you put metal strapping each side of the studs designed for the decoupling forces? Do you consider composite action with the exterior sheathing and then require interior sheathing also for composite action?
Yes, kickers up to the roof structure would be the easiest, but this isn't an option. I look forward to everyone discussion.