Hello, I have issue with part that is in picture below,
I have fixed POM-C shaft and rotational ring from aluminum. As you can see gap between shaft and ring is Φ39-Φ38.8 = 0.2 mm where is contact between them but they ensure rolling of ring on shaft under room temperature without any issues. But when I have temperature around 90°C due to thermal expansion of POM-C and Aluminum critical gap of 0.2 mm is at 90°C 0.115 mm and at this value I got ring stuck and unable to rotate ring unless I cool it below 90°C. Is it root cause in this case that gap between part at value of 0.115 mm is too small and I need to make it bigger or ring should rotate even with gap of 0.115 mm and issue for stuck has different root cause?
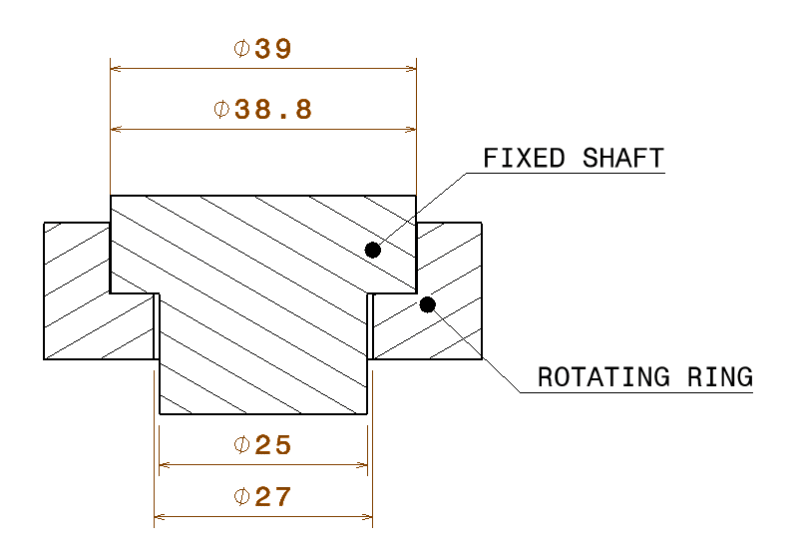
I have fixed POM-C shaft and rotational ring from aluminum. As you can see gap between shaft and ring is Φ39-Φ38.8 = 0.2 mm where is contact between them but they ensure rolling of ring on shaft under room temperature without any issues. But when I have temperature around 90°C due to thermal expansion of POM-C and Aluminum critical gap of 0.2 mm is at 90°C 0.115 mm and at this value I got ring stuck and unable to rotate ring unless I cool it below 90°C. Is it root cause in this case that gap between part at value of 0.115 mm is too small and I need to make it bigger or ring should rotate even with gap of 0.115 mm and issue for stuck has different root cause?