Sajjad2164
Mechanical
I am wondering if I want to apply the load cases involving thermal loads (such as that shown in the photo) and the design temperature is 600 degrees of centigrade (in heat exchanger) and I want to apply the 1.3 safety factor to the loads then what would be the temperature that I'm going to apply to the shell? 780? Do I need to perform the elastic-plastic analysis?
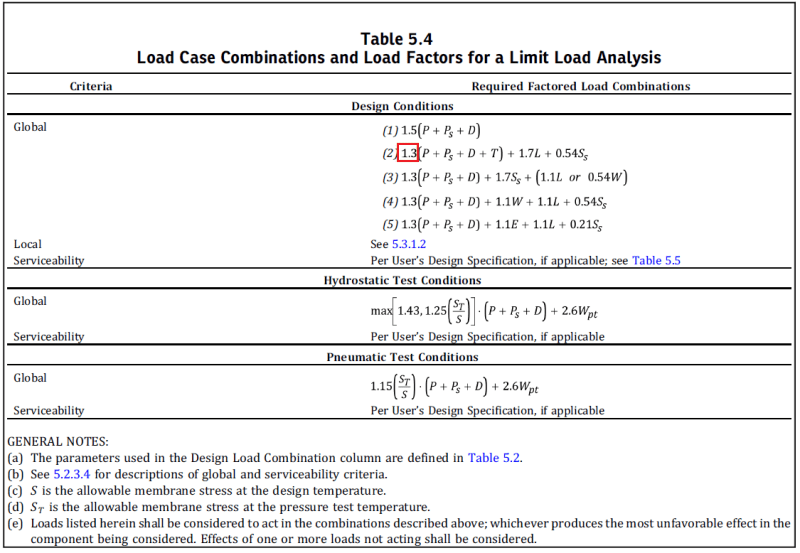