Hello, I have two fluid loops filled with the same coolant mixutre that are circulating in opposite directions. On the left side, there is an engine that is supplying heat to the coolant loop. Immediately after the engine outlet, there is a thermostatic 3 way valve that is diverting 100% of the volume flow back to the engine until the engine reaches its operating temp, To (185F). After which, the volume flow is split and coolant will flow through the outer loop as well. The outer loop has a plate and frame heat exchanger (CHX) followed by an automotive style radiator/fan combo that is electronically controlled by a sensor at To (see dotted line). On the opposite side, there is also a radiator/fan combo that is electronically set to control the temperature at T1 (see dotted line).
Our objective is to measure the amount of heat being transferred across the heat exchanger (CHX) by applying the temperature differential across T1 and T2 to formula Q=rho*Cp*V*deltaT. The radiator on the right side is not always on, when it is not, the heat is removed by the radiator in the left side loop. When the right radiator is on, the left radiator is inactive.
The problem that I am having is that when we are using the right side radiator/fan and heat is being transferred across the heat exchanger, the engine outlet temperature drops. I do not understand why this is happening. The way I am thinking about this is a closed system energy balance problem. Heat in from the engine should equal heat across the heat exchanger which should equal heat across the radiator. Can anyone help explain why the engine outlet temperature drops? Please let me know if you need any more information about the problem. I appreciate any insight that can be provided.
Our objective is to measure the amount of heat being transferred across the heat exchanger (CHX) by applying the temperature differential across T1 and T2 to formula Q=rho*Cp*V*deltaT. The radiator on the right side is not always on, when it is not, the heat is removed by the radiator in the left side loop. When the right radiator is on, the left radiator is inactive.
The problem that I am having is that when we are using the right side radiator/fan and heat is being transferred across the heat exchanger, the engine outlet temperature drops. I do not understand why this is happening. The way I am thinking about this is a closed system energy balance problem. Heat in from the engine should equal heat across the heat exchanger which should equal heat across the radiator. Can anyone help explain why the engine outlet temperature drops? Please let me know if you need any more information about the problem. I appreciate any insight that can be provided.
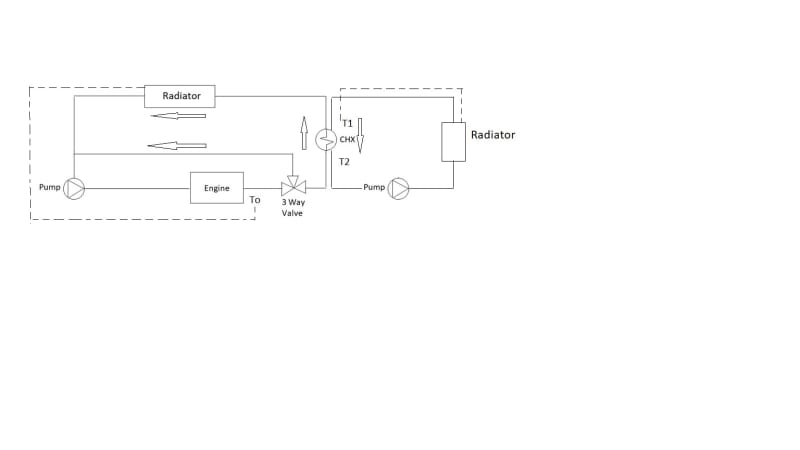