Hi
I am analysing crack-tip to study thickness effect in Elastic Plastic fracture mechanics. Here I have taken two TPB specimen geometry with a/w 0.3 and 0.5 with 10mm and 2.5 mm thickness. I have used 'Tool-Midsurface-Assign thickness and offset' option to specify thickness rather than 'using 'Plane stress/strain thickness=' option in section. I have also given thickness 'from geometry' in 'section assignment'. 4 different input files were created. I used CPS8R plane stress element. but in the result, I get the a/w effect in crack-tip stress-strain analysis and not thickness effect (result in both thicknesses are same). I have attached a pdf with the input file of a/w 0.5 with 2.5 thickness for your reference. I suspect, I have committed some error in my abaqus analysis. Kindly help me in this regards.
I am analysing crack-tip to study thickness effect in Elastic Plastic fracture mechanics. Here I have taken two TPB specimen geometry with a/w 0.3 and 0.5 with 10mm and 2.5 mm thickness. I have used 'Tool-Midsurface-Assign thickness and offset' option to specify thickness rather than 'using 'Plane stress/strain thickness=' option in section. I have also given thickness 'from geometry' in 'section assignment'. 4 different input files were created. I used CPS8R plane stress element. but in the result, I get the a/w effect in crack-tip stress-strain analysis and not thickness effect (result in both thicknesses are same). I have attached a pdf with the input file of a/w 0.5 with 2.5 thickness for your reference. I suspect, I have committed some error in my abaqus analysis. Kindly help me in this regards.
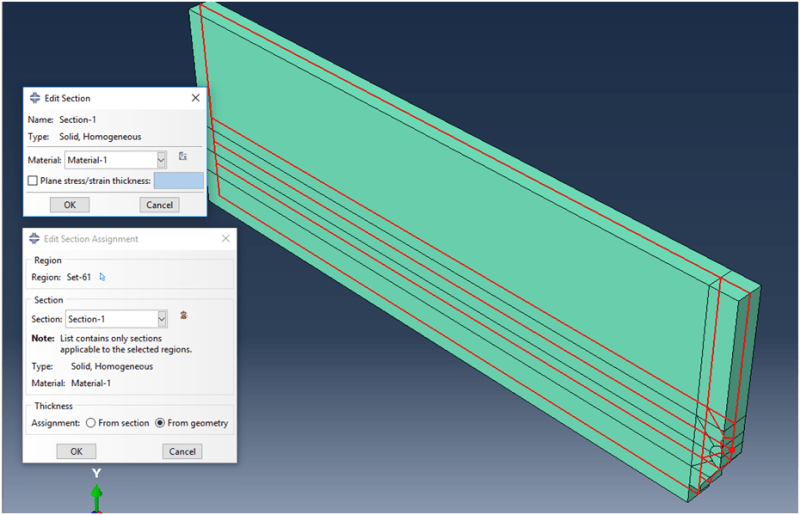
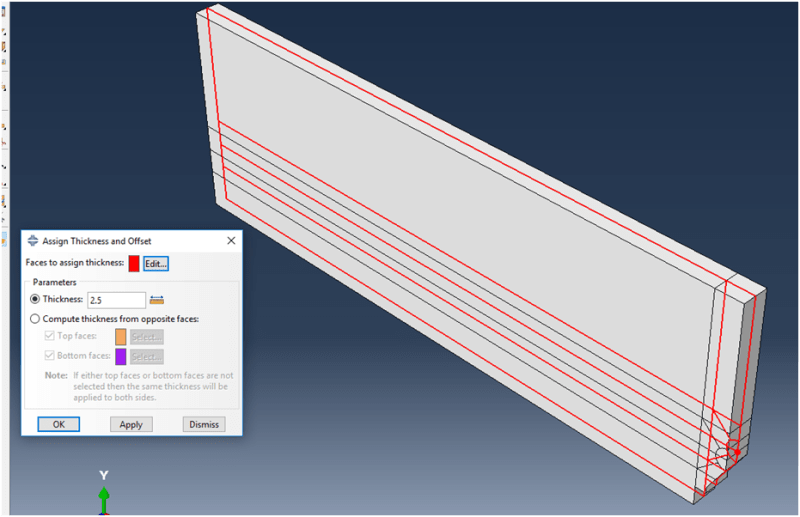
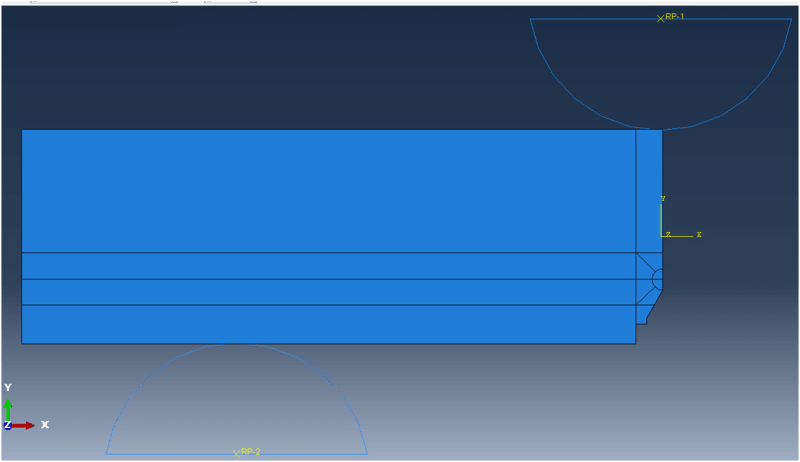