supergee
Mechanical
- Aug 15, 2012
- 77
Hi,
IF I OVER SIMPLIFY There are two approches to dimensioning : one for feature of size and the other on for the rest. Feature of size are feature with two opposed surfaces. hole depth, in that sence are not feature of size. direct tolerancing on the dimension is used on FOS dimensions. everty thing else is controled with geo tolerancing.
in the case of threaded blind holes, there are the thread depth and the tap drill depth. I could imagine using geometric tolerance for neither. I can't find a clear way in y14.5 2018 nor y14.6 2001 to show HOW to tolerance the said depths. can you help? I'm including 4 choices to tolerance the depths.
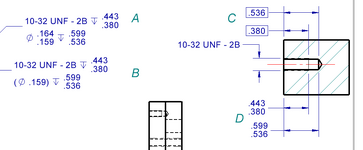
IF I OVER SIMPLIFY There are two approches to dimensioning : one for feature of size and the other on for the rest. Feature of size are feature with two opposed surfaces. hole depth, in that sence are not feature of size. direct tolerancing on the dimension is used on FOS dimensions. everty thing else is controled with geo tolerancing.
in the case of threaded blind holes, there are the thread depth and the tap drill depth. I could imagine using geometric tolerance for neither. I can't find a clear way in y14.5 2018 nor y14.6 2001 to show HOW to tolerance the said depths. can you help? I'm including 4 choices to tolerance the depths.
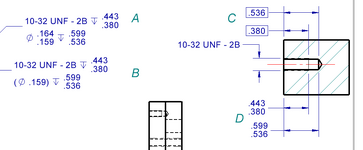