ASHWA
Automotive
- Oct 7, 2020
- 53
thread1103-468608
Dear All,
Had a doubt in Three segment composite tolerance,
In this,
for B Size limit - (73.72 - 73.86 (MMC))
for C Size limit - (13.52 (MMC) - 13.66)
If my B Size = 73.8 & C = 13.6, which got after machining.
Will there be shift in Hole axis?
SME's kindly resolve my doubt.
Thanks.
Dear All,
Had a doubt in Three segment composite tolerance,
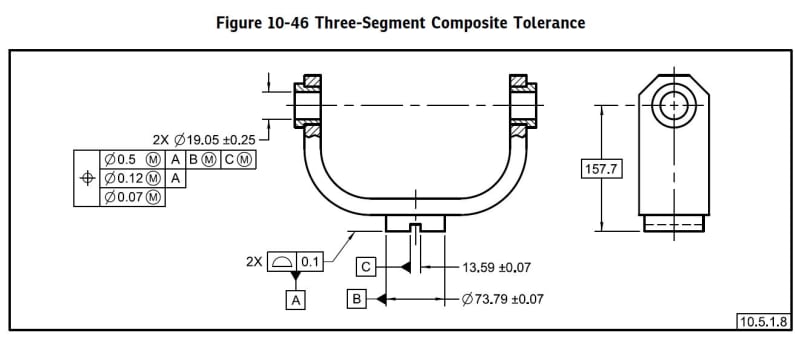
In this,
for B Size limit - (73.72 - 73.86 (MMC))
for C Size limit - (13.52 (MMC) - 13.66)
If my B Size = 73.8 & C = 13.6, which got after machining.
Will there be shift in Hole axis?
SME's kindly resolve my doubt.
Thanks.