Weaverofduart
Agricultural
Hi Peoples,
Now I'm finally getting around to a project that has been on my to do list for ages.
We have been making cider from wild apples for about the last 6 years. As much as 500L per year.
Processing the apples is a huge job so eventually I made a scratter to speed the milling process. That worked so well. We can now mill 1.5t of apples per hour. Problem though is that the 35L press we have been using is now way too small.
So the plan is to build a much larger press of around 350L capacity. Actually a double press with each side capable of ~350L per pressing.
I'm doing a bunch of videos to document the fun which you can find on you tube. There are now 4 in the series but possibly the best one to start you on is where I introduce some of my tool collection. Specifically a bunch of old French and German carpentry tools.
Link
I've got the beams ready to cut and start on the joinery and I've prepared 7 of the 9 posts. So I'm going back and rechecking my engineering in preparation to starting the joinery.
Thats where I've hit a snag.
I've got four timbers that I'll be using for the top and bottom press beams, two at the top two at the bottom.
For the sake of the disscussion lets say these are 10"x10" ea.
I want the press to be able to develop 20t of force to generate 50psi in the press cheese stack which will be ~29" by 29".
P=44,000lbs
A=LxB= 29" x 29" = 841 square inches
S=F/A=44000/841
= 52psi
Horizontal shear in the Beams
V=vertical shear=P/2=22000
A=10 x 10 + 10 x 10 = 200" square
H=3V/2A=3 x 22000 / 2 / 200 = 165psi
There is the problem. The beams are Monterey pine (P. radiata). The figure I have based on the F grades is that the value for shear in beams for F7 timber is 2.1 MPA or ~300psi.
This is WAY above the values given in the timber framing guilds book "Timber Frame Joinery and Design Workbook". There even the strongest timbers tend to be rated way less than this. The strongest is Southern Pine Denser Structural 86 at 145PSI.
So how can I modify these timbers to strengthen them. Vertical steel bolts to increase the resistance to shear? Would adding metal strapping to the tension side of the beams help or would that just increase ability to resist bending but do nothing for shear?
Now I'm finally getting around to a project that has been on my to do list for ages.
We have been making cider from wild apples for about the last 6 years. As much as 500L per year.
Processing the apples is a huge job so eventually I made a scratter to speed the milling process. That worked so well. We can now mill 1.5t of apples per hour. Problem though is that the 35L press we have been using is now way too small.
So the plan is to build a much larger press of around 350L capacity. Actually a double press with each side capable of ~350L per pressing.
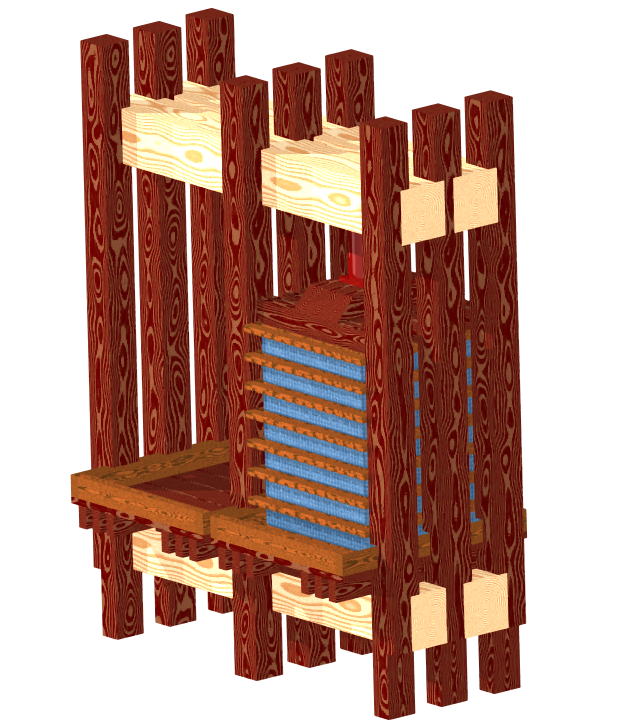
I'm doing a bunch of videos to document the fun which you can find on you tube. There are now 4 in the series but possibly the best one to start you on is where I introduce some of my tool collection. Specifically a bunch of old French and German carpentry tools.
Link
I've got the beams ready to cut and start on the joinery and I've prepared 7 of the 9 posts. So I'm going back and rechecking my engineering in preparation to starting the joinery.
Thats where I've hit a snag.
I've got four timbers that I'll be using for the top and bottom press beams, two at the top two at the bottom.
For the sake of the disscussion lets say these are 10"x10" ea.
I want the press to be able to develop 20t of force to generate 50psi in the press cheese stack which will be ~29" by 29".
P=44,000lbs
A=LxB= 29" x 29" = 841 square inches
S=F/A=44000/841
= 52psi
Horizontal shear in the Beams
V=vertical shear=P/2=22000
A=10 x 10 + 10 x 10 = 200" square
H=3V/2A=3 x 22000 / 2 / 200 = 165psi
There is the problem. The beams are Monterey pine (P. radiata). The figure I have based on the F grades is that the value for shear in beams for F7 timber is 2.1 MPA or ~300psi.
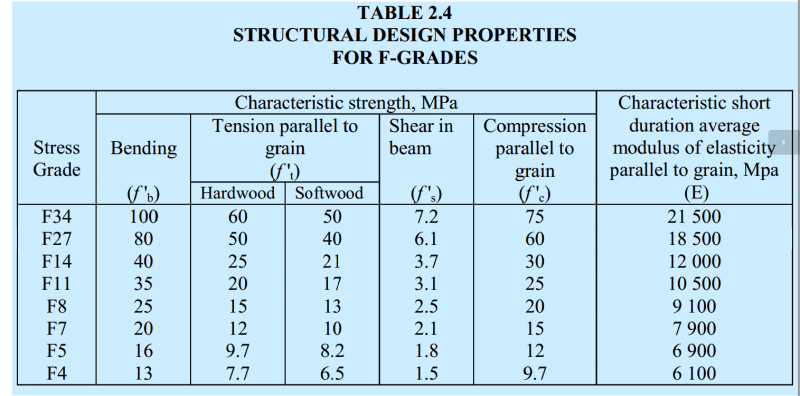
This is WAY above the values given in the timber framing guilds book "Timber Frame Joinery and Design Workbook". There even the strongest timbers tend to be rated way less than this. The strongest is Southern Pine Denser Structural 86 at 145PSI.
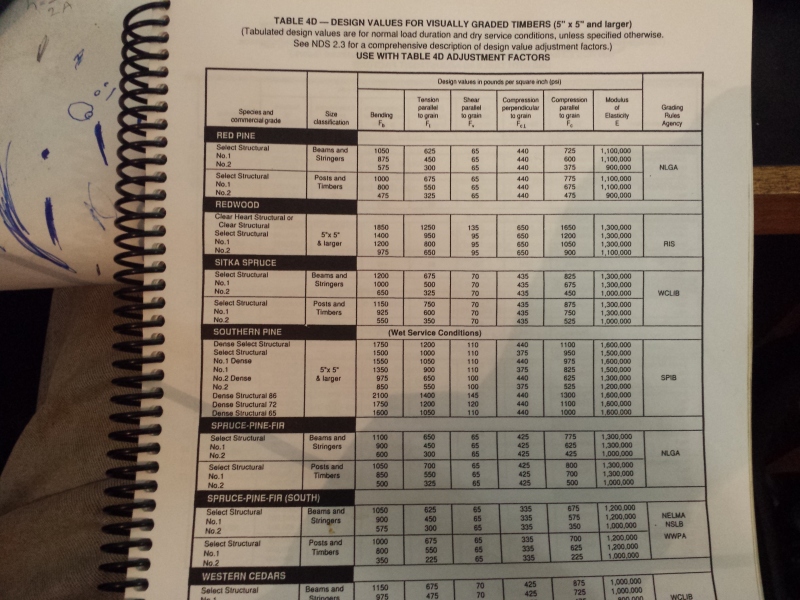
So how can I modify these timbers to strengthen them. Vertical steel bolts to increase the resistance to shear? Would adding metal strapping to the tension side of the beams help or would that just increase ability to resist bending but do nothing for shear?