SBRIRONMAN
Mechanical
To all,
I have several drawings that I am checking for our engineering group and the source that
is making the drawings has GDT on a specific tapped hole.
I need some insight to his GDT callout on the tapped hole circled in red.Better yet,
and explanation why : true position / dia 0.6 / max material condition / c /d/ e
/ dia 0.3 / max materialcondition / c
If someone can maybe explain what he means by this, I would appreciate it. I do not want
to send the drawing back to (China ) and have them remove the GDT if it is not necessary.
Thanks
I have several drawings that I am checking for our engineering group and the source that
is making the drawings has GDT on a specific tapped hole.
I need some insight to his GDT callout on the tapped hole circled in red.Better yet,
and explanation why : true position / dia 0.6 / max material condition / c /d/ e
/ dia 0.3 / max materialcondition / c
If someone can maybe explain what he means by this, I would appreciate it. I do not want
to send the drawing back to (China ) and have them remove the GDT if it is not necessary.
Thanks
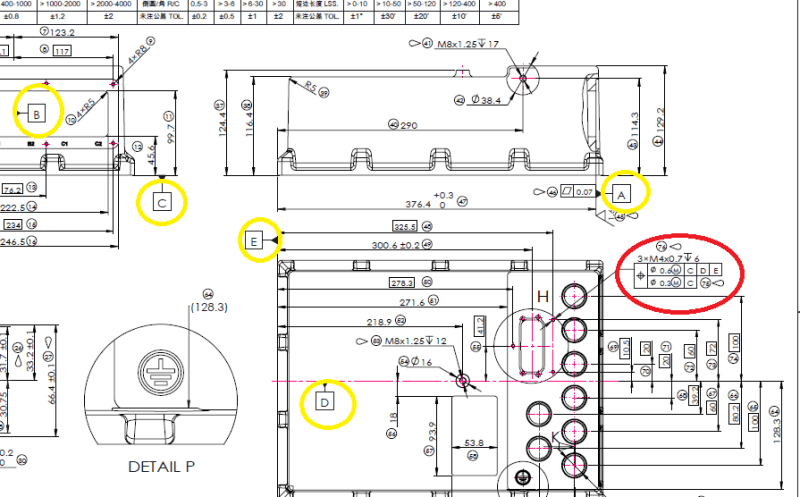