NickParker
Electrical
- Sep 1, 2017
- 444
The generator vendor cannot meet the ABS requirement for momentary transient voltage variations for the step load of 60% of the generator's rated current. However, these voltage variation requirements can be met for a step load of 33%, which aligns with the diesel engine's maximum step load capacity (sudden load steps of 0-33%-67%-100%, in three steps).
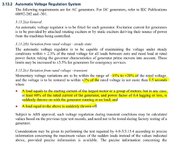
Given this, I believe the deviation from the generator vendor is acceptable.
Any opinions?
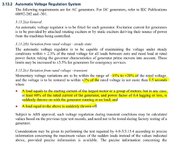
Given this, I believe the deviation from the generator vendor is acceptable.
Any opinions?