Sajjad2164
Mechanical
Hello, friends!
I am told to perform a finite element analysis for a transportation process of a special vessel. The model includes trunnions and a tailing lug. For the shell, I executed the linearization process and compare the results with allowable values given in ASME-SecII, Part D, but I am wondering what allowable limit should I use for the structural attachments such as the body of trunnion and tailing lugs? I appreciate any guides in the process.
Thanks
I am told to perform a finite element analysis for a transportation process of a special vessel. The model includes trunnions and a tailing lug. For the shell, I executed the linearization process and compare the results with allowable values given in ASME-SecII, Part D, but I am wondering what allowable limit should I use for the structural attachments such as the body of trunnion and tailing lugs? I appreciate any guides in the process.
Thanks
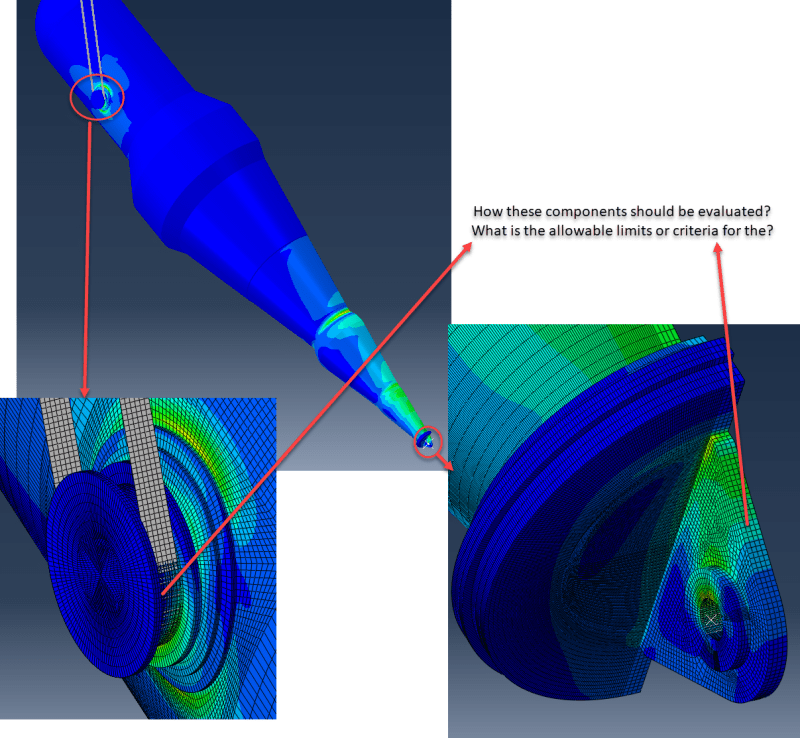