Rwelch9
Mechanical
- Apr 22, 2020
- 116
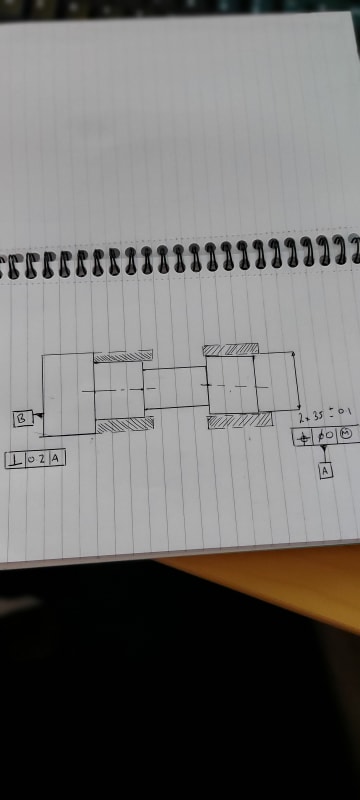
Hi
Please find attached sketch ,
The sketch is simply to illustrate a 2x cylindrical shaft diameter as a common datum.
My question , as most of you guys are aware my experience with true geometric counterparts is limited. ( due to most of my inspection experience is on a CMM )
As this is a 2x will the geometric counter part be like a bush that would touch an mate against the most outer points of the two cylinders ?
I have done the sketch to show a potential issue where by machining flaws or another reason the front shaft diameter is slightly tapered to the other one.
I am trying to understand if this scenario happened or the front cylinder axis was just 0.04 off center , how does this affect the geometric counter part to derive a common axis between the two cylinders .
Thanks