Good morning, Everyone.
I am trying to understand buckling factor analysis results. I've made this 11m truss and considered both top and bottom chords will be conected to a column. I have considered translation in all directions as fixed and rotation in the x axis restricted too. My analysis is made with a self weight Load and three uplift loads.
For the results of the first mode I have this
Buckling factor of : -53.542
From my understandment, what this means is that for this mode buckling would be based on reverse loading.
Then I have the second mode:
Buckling factor of : 162.3229
And the compression on the bottom chord is: 0,25kN
This means that for my bottom chord the Critical buckling load Ne is equal to: 0,25*162,3229 = 40kN
I would like to know if my understandment of those factors are at the right direction or if I am missing something.
I am trying to understand buckling factor analysis results. I've made this 11m truss and considered both top and bottom chords will be conected to a column. I have considered translation in all directions as fixed and rotation in the x axis restricted too. My analysis is made with a self weight Load and three uplift loads.
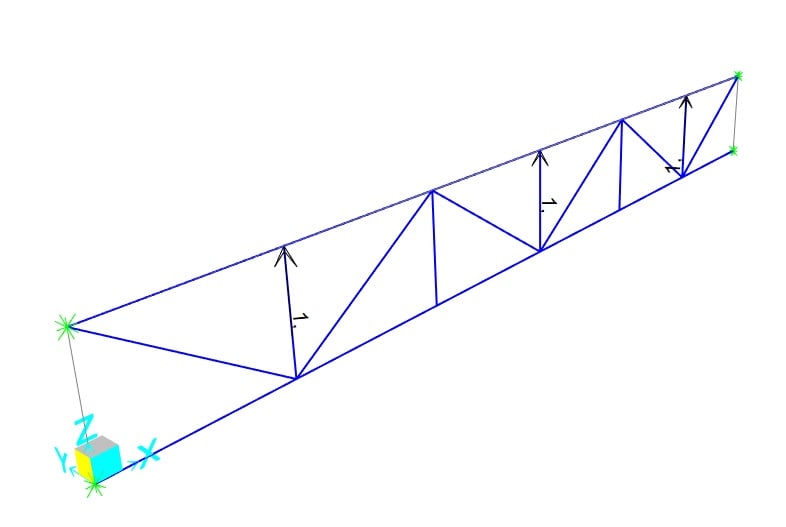
For the results of the first mode I have this
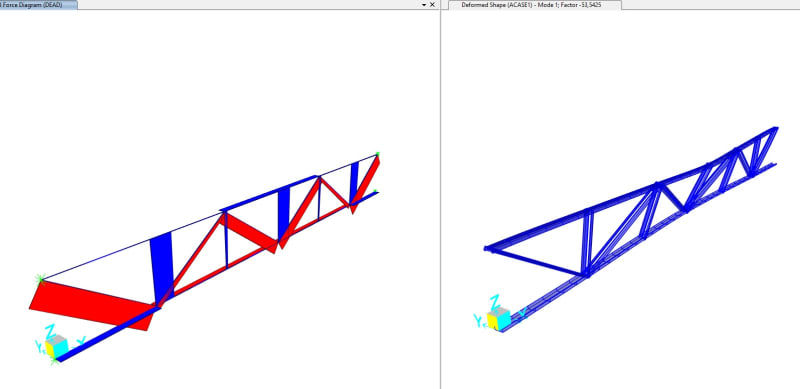
Buckling factor of : -53.542
From my understandment, what this means is that for this mode buckling would be based on reverse loading.
Then I have the second mode:
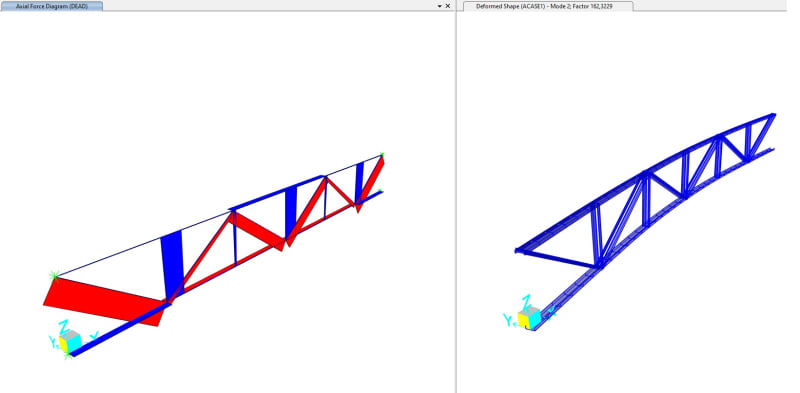
Buckling factor of : 162.3229
And the compression on the bottom chord is: 0,25kN
This means that for my bottom chord the Critical buckling load Ne is equal to: 0,25*162,3229 = 40kN
I would like to know if my understandment of those factors are at the right direction or if I am missing something.