LeRepeteur
Mechanical
Yo,
I'm currently running a simulation on a fully symmetric assembly, all other weak spots are symetric on each side except here. The force is acting at the front most point of the assembly and is in the center where the blue dot is. Just trying to figure out why it is so unsymmetrical.
Cheers,
LR
I'm currently running a simulation on a fully symmetric assembly, all other weak spots are symetric on each side except here. The force is acting at the front most point of the assembly and is in the center where the blue dot is. Just trying to figure out why it is so unsymmetrical.
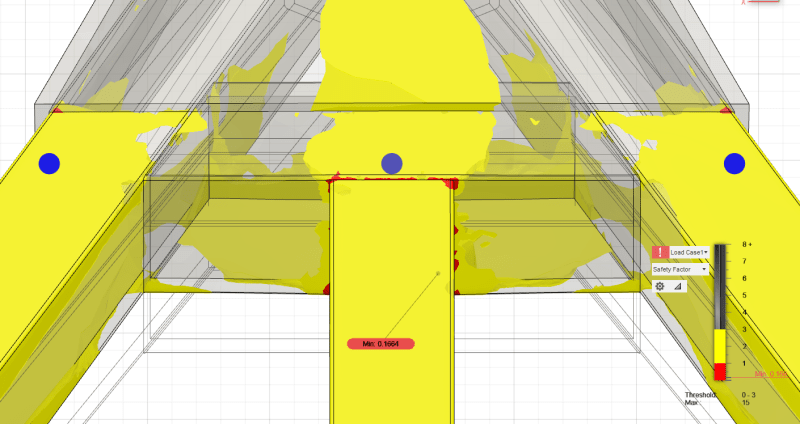
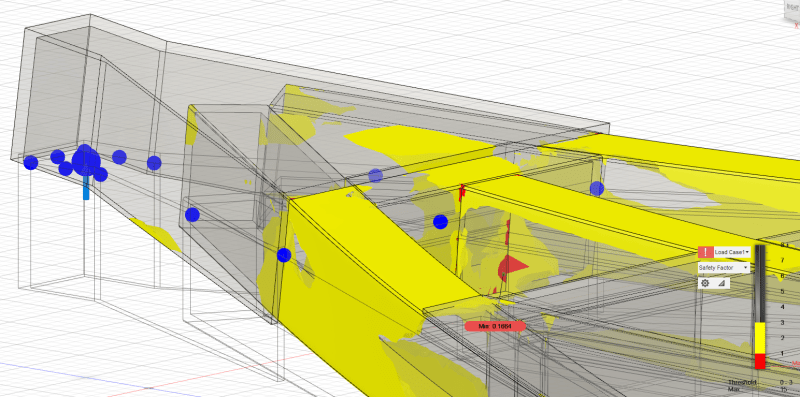
Cheers,
LR