Aniruddah ALam
Mechanical
- Mar 14, 2025
- 1
Hello everyone,
I am currently facing issues with my Abaqus simulation and would greatly appreciate any insights from the community. Below is a detailed explanation of my setup, the troubleshooting steps I have taken, and the problems I am still encountering.
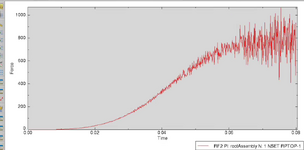
Ran the simulation on GPU instead of HPC (.inp-based run) → Some improvement in smoothness but still issues at later time steps.
Reduced velocity to 5 mm/s instead of 1000 mm/s → Helped make the reaction force curve smoother but modulus is still unrealistic.
Increased total simulation time to 1s → Some improvement, but oscillations remain at later stages.
Applied all boundary conditions at Step-1 instead of the initial step → No significant improvement.
Used mass scaling (1,600,000) for the lattice set → Helped speed up the simulation but didn’t resolve force fluctuations.
Potential Causes I Suspect:
Boundary conditions: Is my method of calculating strain (U2 displacement / total lattice length) appropriate for this setup?
What could be causing the unstable reaction force curve despite all these corrections?
Why is the calculated elastic modulus so unrealistically high?
What additional steps should I take to troubleshoot this problem?
I would be extremely grateful for any insights or recommendations from experts in Abaqus HPC simulations, parallel processing, and nonlinear material behavior. Thank you in advance for your time and support!
Best regards,
Aniruddah
I am currently facing issues with my Abaqus simulation and would greatly appreciate any insights from the community. Below is a detailed explanation of my setup, the troubleshooting steps I have taken, and the problems I am still encountering.
Simulation Setup:
- Model Type: Auxetic Lattice structure
- Computation: Running on a High-Performance Cluster (HPC) using multiple processors
- An “Explicit, Dynamics” analysis was chosen to replicate the quasi-static compression response.
- Lattice Dimensions:
- Total length in the Y-direction: 41.6 mm
- Load applied at the top surface, couple constrained applied
- Boundary Conditions:
- To simulate the actual experimental boundary conditions, two reference points were defined on the planes of the top and bottom surfaces in the loading direction.
- Velocity applied: -1000 mm/s in the Y-direction at the Top Reference Point.
- Velocities and angular velocities and degrees of freedom were restricted in the X- and Z-axes
- A coupling constraint was applied between the top and bottom reference points and the corresponding boundary surfaces, ensuring that all nodes on the surface shared the same boundary conditions when these conditions were applied to the reference points.
- Using Amp-1 amplitude, a smooth loading amplitude was employed to ensure that the system did not retain any kinetic energy at the beginning of the simulation
- Encastre BC applied at the bottom surface.
- Material Properties:
- Material: Nylon 2200
- Young’s modulus: 1140 MPa
- Poisson’s ratio: 0.3
- Simulation Parameters:
- Step duration: 0.04 s
- Contact properties: A general explicit contact was defined at the initial step to prevent self-penetration of the lattice structure. The contact had a penalty friction coefficient of 0.3 in the tangential direction and hard contact in the normal direction.
Problems Encountered:
1. Unstable Reaction Force Curve
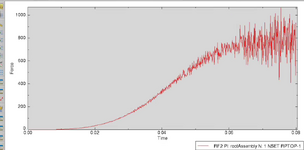
- Initially, I obtained a highly fluctuating reaction force (RF-2) curve, making it difficult to analyze the results.
- The fluctuations became less severe when I reduced the applied velocity from 1000 mm/s to 5 mm/s.
- However, even after applying mass scaling and running for a longer time (1s instead of 0.4s), the reaction force still starts oscillating significantly in the later stages of the simulation.
2. Unrealistic Elastic Modulus
- I calculated stress by dividing the reaction force by the load-bearing top surface area.
- I calculated strain by dividing the U2 displacement of the reference point by the total lattice length in the Y-direction.
- However, the elastic modulus (stress/strain) is extremely high (~220 GPa), while I was expecting 100-200 MPa, based on the literature.
- Given that my material's Young’s modulus is only 1140 MPa, this value seems completely unrealistic.
Ran the simulation on GPU instead of HPC (.inp-based run) → Some improvement in smoothness but still issues at later time steps.




Potential Causes I Suspect:

Seeking Advice:



I would be extremely grateful for any insights or recommendations from experts in Abaqus HPC simulations, parallel processing, and nonlinear material behavior. Thank you in advance for your time and support!
Best regards,
Aniruddah