I have a 41-pin thermocouple (type K) feed-thru flange for connecting a multipair thermocouple extension cable from within a vessel to the outside. The multipair cable has an overall shield and drain wire. I have 5 spare pins on the feed-thru flange; 3 are chromel (+) and 2 are aluminel (-). I want to use one of the spare pins to bring my drain wire across. I don't have any other way except the feed-thru flange for bringing the drain wire across. There's potential for noise and would like to use the drain wire for this purpose. Do you see any issues with this? Please provide feedback.
Thank you!
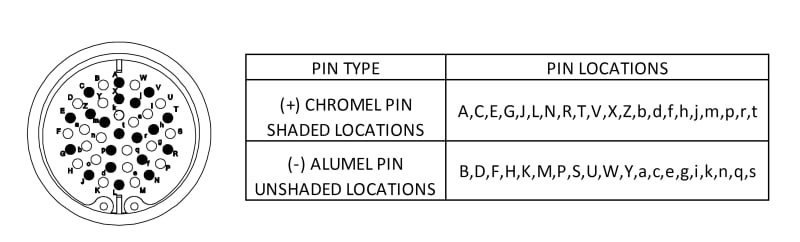
Thank you!