Christo_AU
Structural
- Sep 4, 2023
- 20
Good day
I am not very experienced with the design of powertrain parts and would appreciate any help.
I have designed a v-belt and pulley assembly, please see the picture below. The load (platform lifted with screws) is normally driven by a servo motor. In case of a power failure, the platform can be lowered with a hand crank or hand drill connected to a 1/2 inch socket. The socket is on one end of the pulley assembly. So the pulley assembly will normally not be transmitting any power, but will always run (no clutch). This system will only run for 5 minutes, twice a day, 5 days per week. Service life is 10 years, so total is about 217 hours.
A fitter is concerned that the v-belt will wear out pretty quickly. I asked why but he didnt provide details, other than "sh** design". I assume it might be becuase the idler/tensioners push on the back of the v-belt. Note the v-belt is cogged.
Will this v-belt last for 200 hours of operation at 1630 RPM over 10 years? If not, any guesses as to how long it might last?
Thank you in advance.
Christo
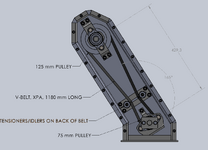
I am not very experienced with the design of powertrain parts and would appreciate any help.
I have designed a v-belt and pulley assembly, please see the picture below. The load (platform lifted with screws) is normally driven by a servo motor. In case of a power failure, the platform can be lowered with a hand crank or hand drill connected to a 1/2 inch socket. The socket is on one end of the pulley assembly. So the pulley assembly will normally not be transmitting any power, but will always run (no clutch). This system will only run for 5 minutes, twice a day, 5 days per week. Service life is 10 years, so total is about 217 hours.
A fitter is concerned that the v-belt will wear out pretty quickly. I asked why but he didnt provide details, other than "sh** design". I assume it might be becuase the idler/tensioners push on the back of the v-belt. Note the v-belt is cogged.
Will this v-belt last for 200 hours of operation at 1630 RPM over 10 years? If not, any guesses as to how long it might last?
Thank you in advance.
Christo
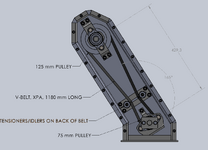