mcmg
Chemical
- Feb 3, 2016
- 4
Hi. I've read a lot of valuable information regarding this topic on this forum, but I am still quite bothered with the problem I am currently handling. Hope you can all help me. Posted this topic too on cheresources.
The scenario is: A closed loop system with 46wt% water and 54wt% ethylene glycol used for cooling the process side: a pump takes in -20C liquid from a tank (both at ground) and supplies the liquid to 2 heat exchangers (HE1, HE2) located approximately +12m above ground. The outlet fluid (-14C) is used as cooling jacket fluid for accumulator tanks (T1, T2) located below the exchanger (located at ~8m above ground). The exiting fluid from these T1/T2 (at -10C) flows to a refrigeration system located at ground to cool back the fluid to -20C. This goes back to the tank (N2 blanketed and vented to atm), via dip pipe (all the way below near the tank bottom).
Observations and Data:
1. By design, the flow rate should be approximately ~18,000 kg/hr and discharge pressure at pump should be ~320 kpag. However, the flow we are getting is ~25,000 kg/hr and discharge pressure is 230 kpag. We tried to throttle the valve outlet of the pump, and we are still experiencing high flows as compared with the theoretical (even if the valve was nearly 80% closed).
2. We conducted pressure profiling of the system and was surprised by appearance of vacuum at certain points (at elevation of 7.4m). However, at top point (HE1, HE2), pressure was ~100 kpag. Temperature during this time was <-20C.
3. The vacuum pressure was -35 kpag. Fluid temperature at that time we got that value was 10C (ref unit was just shut down). When we opened the points, we experienced a drop in flow rate (from 27,000 to ~25,000 kg/hr).
4. At fluid temperature 35C, we opened up the drain points again, we experienced alternate vacuuming and liquid draining (every 5s) for system 1 (T1) and continuous discharge for system 2 (T2). The flow dropped again to ~25,00 kg/hr (from 27,000 kg/hr), discharge pressure increased to 220 kpag (from 200 kpag). We then tried to throttle the pump discharge valve while both drain valves were still opened to atmosphere. We did not see any changes in the discharge pressure and flowrates.
5. In all tests, we do not observe any pump vibration.
Questions:
1. What cause/s the vacuum pressures in the line?
- My initial guess is that siphoning effect is occurring. And such, the higher flow rate. On theoretical calculations (assuming allowed design DP across the heat exchangers), I should only get ~1 bar dP across the system, but my pump is designed for ~3bar dP, hence higher flow. Is it correct to assume that my line is "fully filled" and the equations I used are valid?
- I back calculated from discharge point (where I used back Pressure = static head of liquid) and got some vacuum pressure value, and should not pose for any vaporization at low temperature, VP is almost 0 barg.
2. Should I be concerned with the appearance of vacuum pressures in the system if my system is attaining more flow? Velocity concerns and or vacuum concerns for my piping and equipment?
3. Most puzzling for me is that with increase in temperature I did get some vacuuming and discharging actions on the drain valves which I have not experienced with the cold temperature. I checked on the vapor pressure and at 35C is -0.95 barg. Flow rate was higher (which on reading references, higher flowrates should "flush out" the vapor in the system, if any). I am assuming that this may be due to "relatively lower back pressure on the discharge end" as the density is relatively lower at 35C. Is there any relation to viscosity changes (Nre at low temp <10,000 vs Nre 35C >50,000).
It's quite a lengthy description, but thanks in advance to everyone.
The scenario is: A closed loop system with 46wt% water and 54wt% ethylene glycol used for cooling the process side: a pump takes in -20C liquid from a tank (both at ground) and supplies the liquid to 2 heat exchangers (HE1, HE2) located approximately +12m above ground. The outlet fluid (-14C) is used as cooling jacket fluid for accumulator tanks (T1, T2) located below the exchanger (located at ~8m above ground). The exiting fluid from these T1/T2 (at -10C) flows to a refrigeration system located at ground to cool back the fluid to -20C. This goes back to the tank (N2 blanketed and vented to atm), via dip pipe (all the way below near the tank bottom).
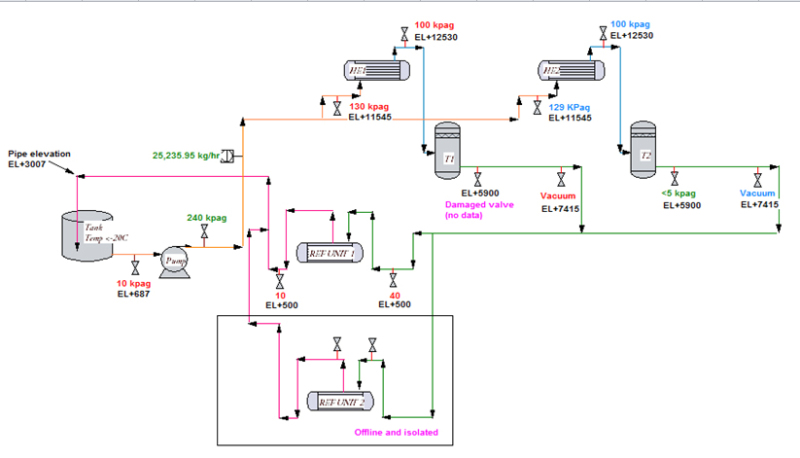
Observations and Data:
1. By design, the flow rate should be approximately ~18,000 kg/hr and discharge pressure at pump should be ~320 kpag. However, the flow we are getting is ~25,000 kg/hr and discharge pressure is 230 kpag. We tried to throttle the valve outlet of the pump, and we are still experiencing high flows as compared with the theoretical (even if the valve was nearly 80% closed).
2. We conducted pressure profiling of the system and was surprised by appearance of vacuum at certain points (at elevation of 7.4m). However, at top point (HE1, HE2), pressure was ~100 kpag. Temperature during this time was <-20C.
3. The vacuum pressure was -35 kpag. Fluid temperature at that time we got that value was 10C (ref unit was just shut down). When we opened the points, we experienced a drop in flow rate (from 27,000 to ~25,000 kg/hr).
4. At fluid temperature 35C, we opened up the drain points again, we experienced alternate vacuuming and liquid draining (every 5s) for system 1 (T1) and continuous discharge for system 2 (T2). The flow dropped again to ~25,00 kg/hr (from 27,000 kg/hr), discharge pressure increased to 220 kpag (from 200 kpag). We then tried to throttle the pump discharge valve while both drain valves were still opened to atmosphere. We did not see any changes in the discharge pressure and flowrates.
5. In all tests, we do not observe any pump vibration.
Questions:
1. What cause/s the vacuum pressures in the line?
- My initial guess is that siphoning effect is occurring. And such, the higher flow rate. On theoretical calculations (assuming allowed design DP across the heat exchangers), I should only get ~1 bar dP across the system, but my pump is designed for ~3bar dP, hence higher flow. Is it correct to assume that my line is "fully filled" and the equations I used are valid?
- I back calculated from discharge point (where I used back Pressure = static head of liquid) and got some vacuum pressure value, and should not pose for any vaporization at low temperature, VP is almost 0 barg.
2. Should I be concerned with the appearance of vacuum pressures in the system if my system is attaining more flow? Velocity concerns and or vacuum concerns for my piping and equipment?
3. Most puzzling for me is that with increase in temperature I did get some vacuuming and discharging actions on the drain valves which I have not experienced with the cold temperature. I checked on the vapor pressure and at 35C is -0.95 barg. Flow rate was higher (which on reading references, higher flowrates should "flush out" the vapor in the system, if any). I am assuming that this may be due to "relatively lower back pressure on the discharge end" as the density is relatively lower at 35C. Is there any relation to viscosity changes (Nre at low temp <10,000 vs Nre 35C >50,000).
It's quite a lengthy description, but thanks in advance to everyone.