I have a situation where I need to support some heavy precast concrete trough covers (lids) along a cast in place concrete wall. The covers are 200 mm (8") thick and will support pedestrian loading as well as some vehicle loads. They also need to be removable to inspect the trough below. Due to various constraints, I only have about 50 mm (2") of bearing width between the cover and the wall as shown below. Also, the clear space within the trough cannot be encroached on, so there is no possibility of supporting the covers on a ledge or bracket.
I have a few concerns: (1) bearing failure at the edge of the cover or wall with possibility of a diagonal crack forming; (2) anchorage of the reinforcement; (3) general wear and tear around the edges of the concrete as the lids are occasionally lifted and replaced and shifted around.
My concept is sketched below. I believe the only way of doing this would be to cast in some steel angles that would be anchored into the respective concrete elements with welded reinforcement. But this would require a lot of welding, which might be problematic.
Is there a better way of doing this that doesn't involve so much welding?
I have a few concerns: (1) bearing failure at the edge of the cover or wall with possibility of a diagonal crack forming; (2) anchorage of the reinforcement; (3) general wear and tear around the edges of the concrete as the lids are occasionally lifted and replaced and shifted around.
My concept is sketched below. I believe the only way of doing this would be to cast in some steel angles that would be anchored into the respective concrete elements with welded reinforcement. But this would require a lot of welding, which might be problematic.
Is there a better way of doing this that doesn't involve so much welding?
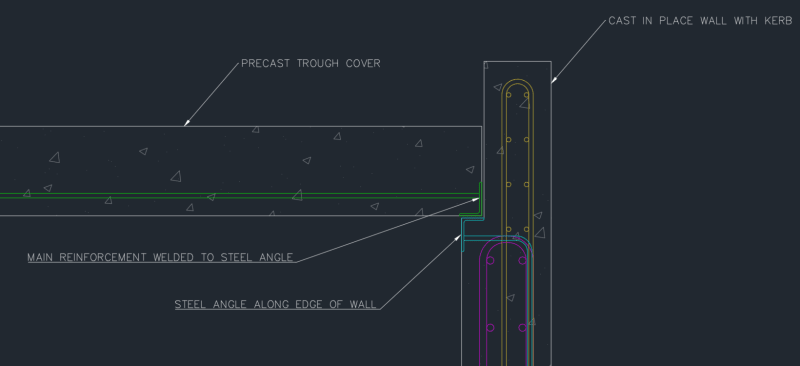