JazzSinatra
Mechanical
What is your opinion about using very loose tolerances on non-critical or functionally inexact features? I use the following simple and fictitious hole as an example:
Let's say that the location of the hole in the picture is non-critical, so it can be anywhere on the surface of that beam, but it must not break the edges of the beam. Is it bad or confusing practice to actually dimension a feature to its functional limits (as in the picture) or should it just be defined by general tolerances, when feature is non-critical or inexact? I think that in consumer products it could give bad impression of quality, if pieces don't look always same, but for in-house products, a machinist wouldn't need to reject or ask, if the hole would for some reason be a bit off. Any thoughts about this?
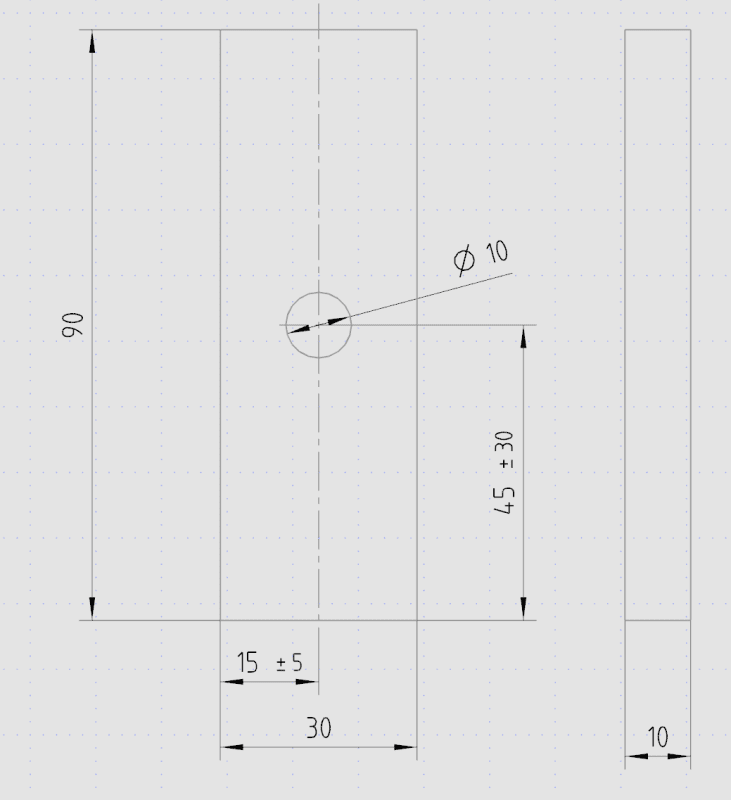
Let's say that the location of the hole in the picture is non-critical, so it can be anywhere on the surface of that beam, but it must not break the edges of the beam. Is it bad or confusing practice to actually dimension a feature to its functional limits (as in the picture) or should it just be defined by general tolerances, when feature is non-critical or inexact? I think that in consumer products it could give bad impression of quality, if pieces don't look always same, but for in-house products, a machinist wouldn't need to reject or ask, if the hole would for some reason be a bit off. Any thoughts about this?