I have an Altivar 312 VFD running a 24" radial arm saw. (7.5hp) Besides just generally engaging one's fight-or-flight its got two problems.
1) The customer complained of a "bad smell" which I tracked down to a burnt-out braking resistor that charred the enclosure paint into a burn waffle pattern under it.
and
2) When turned ON the saw ramps up to (terror speed) sits there for about 4 seconds then ramps down to about to about a hundred RPM and sits there for about 4 seconds then ramps back up to speed. Constantly cycling this way. There's no speed control involved - you turn the saw ON and it accels up to the VFD parameter speed (10sec) and when you're done you hit stop and it decels (15 seconds) and stops.
The saw's normal ops are turn it ON power-feed it thru a bunch of aluminum, hit stop, unload the material, index the feed stock, screw around getting it all lined up and jigged in, and after 2~3 minutes the cycle is repeated. So a 3 minute start stop cycle. This has gone on for a year. I'm wondering if the resistor has always been threatened and finally died or if this bizarre cycling thrashed it. They indicated they smelled something funny tried to find it in the whole shop gave up and when they attempted to use the saw discovered this cycling behavior.
One last bit of info. When it does this cycling as soon as the saw gets to high speed the display switches from Hertz to "OVERBRAKING" fault then the slowdown occurs. What's causing this cycling?!
Keith Cress
kcress -
1) The customer complained of a "bad smell" which I tracked down to a burnt-out braking resistor that charred the enclosure paint into a burn waffle pattern under it.
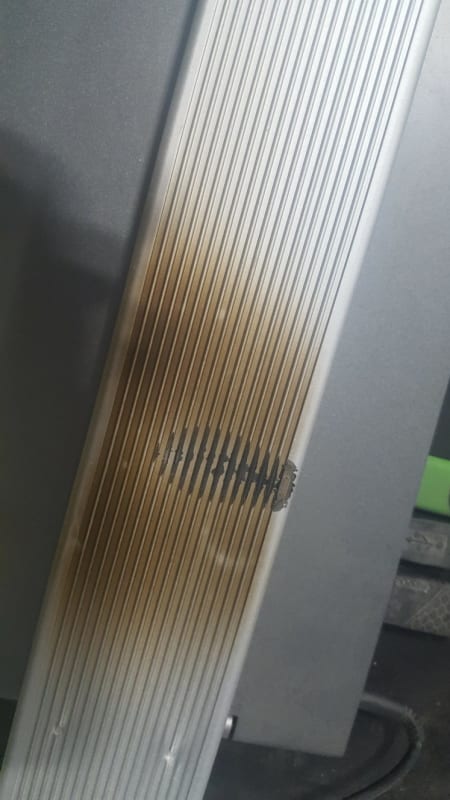
and
2) When turned ON the saw ramps up to (terror speed) sits there for about 4 seconds then ramps down to about to about a hundred RPM and sits there for about 4 seconds then ramps back up to speed. Constantly cycling this way. There's no speed control involved - you turn the saw ON and it accels up to the VFD parameter speed (10sec) and when you're done you hit stop and it decels (15 seconds) and stops.
The saw's normal ops are turn it ON power-feed it thru a bunch of aluminum, hit stop, unload the material, index the feed stock, screw around getting it all lined up and jigged in, and after 2~3 minutes the cycle is repeated. So a 3 minute start stop cycle. This has gone on for a year. I'm wondering if the resistor has always been threatened and finally died or if this bizarre cycling thrashed it. They indicated they smelled something funny tried to find it in the whole shop gave up and when they attempted to use the saw discovered this cycling behavior.
One last bit of info. When it does this cycling as soon as the saw gets to high speed the display switches from Hertz to "OVERBRAKING" fault then the slowdown occurs. What's causing this cycling?!
Keith Cress
kcress -