Hello,
So attached I have a photo of a tentative motor (0.37 kW, 4 pole, 3 phase, rated speed = 1705 RPM, rated torque = 2.07 Nm). I also have my load. I aim to use a VFD, as my load Is over a range of speeds. Using a V/Hz ratio of 7.67 I have worked out that my rated motor torque will stick at 2.07 Nm regardless of the frequency (or synchronous speed) that I set the motor.
Under this logic my motor will not be able to provide enough rated torque at the lower speeds, however the peak torque is still above the load (sticking at 5.5 Nm for different frequencies). Is this OK to do?
The grey line is the motor curve at 60 Hz. The yellow curve is the load. I also know that things can get a bit funny below a 20 Hz frequency...
The only other option I can see is to pick a larger motor with a rated torque of around 5 Nm (for max load). Even then, my motor will have a much larger torque than is required at most frequencies and I am afraid I will end up accelerating the load.
Kind regards
Patrick
So attached I have a photo of a tentative motor (0.37 kW, 4 pole, 3 phase, rated speed = 1705 RPM, rated torque = 2.07 Nm). I also have my load. I aim to use a VFD, as my load Is over a range of speeds. Using a V/Hz ratio of 7.67 I have worked out that my rated motor torque will stick at 2.07 Nm regardless of the frequency (or synchronous speed) that I set the motor.
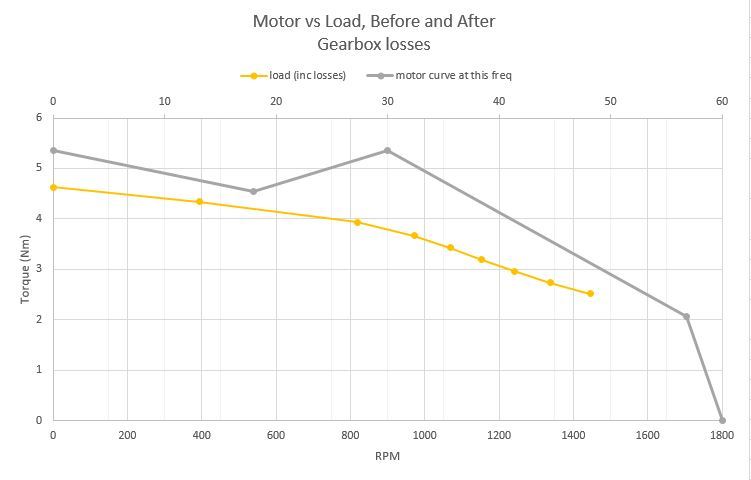
Under this logic my motor will not be able to provide enough rated torque at the lower speeds, however the peak torque is still above the load (sticking at 5.5 Nm for different frequencies). Is this OK to do?
The grey line is the motor curve at 60 Hz. The yellow curve is the load. I also know that things can get a bit funny below a 20 Hz frequency...
The only other option I can see is to pick a larger motor with a rated torque of around 5 Nm (for max load). Even then, my motor will have a much larger torque than is required at most frequencies and I am afraid I will end up accelerating the load.
Kind regards
Patrick