Rocket2M
Mechanical
- Sep 12, 2021
- 2
Hi guys,
I'm currently having a problem with my VTP. Pumping service is for seawater with high static head application (about 13 to 19 m depending on tidal). The impeller material is nickel-aluminium-bronze (NAB) while the shaft and coupling material is monel k400. Pump design is closed, diffuser type with radial flow impeller and consist of 2 stage impeller. Sodium hypochlorite is injected into the well every week for 20L. We recently pull this out as we received report of no flow pumping and found lineshaft has parted near the coupling section (key type) and spider has torsioned, splitted from its flange. Found minor cavitation on inlet vane of 2nd stage and minor pitting on outlet vane, not sure due to cavitation or not. Whole line shaft was found pitting and runout out of tolerance. Found out-of-straightness as well. The spider bearing design is having two sleeve, one monel on the shaft, and the other is vesconite in between monel sleeve and NAB spider bearing. No vibration monitoring and protection is installed as this pump is originally only used to provide seawater in case of emergency and is engine driven by right angle gearbox. For the past few months however, this pump has been routinely run to overboard line (which is sized for pump minimum flow). Seek expert opinion on what could be contributing to the development of this case. For me I personally think that running near low flow region caused higher vibration and accelerated bearing wear of the pump, subsequently causing wobbling and pump running out of concentricity and causing torsion of the spider. Afterwards as spider has failed, lineshaft has no radial support for deflection and parted. Please let me know what do you think
I'm currently having a problem with my VTP. Pumping service is for seawater with high static head application (about 13 to 19 m depending on tidal). The impeller material is nickel-aluminium-bronze (NAB) while the shaft and coupling material is monel k400. Pump design is closed, diffuser type with radial flow impeller and consist of 2 stage impeller. Sodium hypochlorite is injected into the well every week for 20L. We recently pull this out as we received report of no flow pumping and found lineshaft has parted near the coupling section (key type) and spider has torsioned, splitted from its flange. Found minor cavitation on inlet vane of 2nd stage and minor pitting on outlet vane, not sure due to cavitation or not. Whole line shaft was found pitting and runout out of tolerance. Found out-of-straightness as well. The spider bearing design is having two sleeve, one monel on the shaft, and the other is vesconite in between monel sleeve and NAB spider bearing. No vibration monitoring and protection is installed as this pump is originally only used to provide seawater in case of emergency and is engine driven by right angle gearbox. For the past few months however, this pump has been routinely run to overboard line (which is sized for pump minimum flow). Seek expert opinion on what could be contributing to the development of this case. For me I personally think that running near low flow region caused higher vibration and accelerated bearing wear of the pump, subsequently causing wobbling and pump running out of concentricity and causing torsion of the spider. Afterwards as spider has failed, lineshaft has no radial support for deflection and parted. Please let me know what do you think
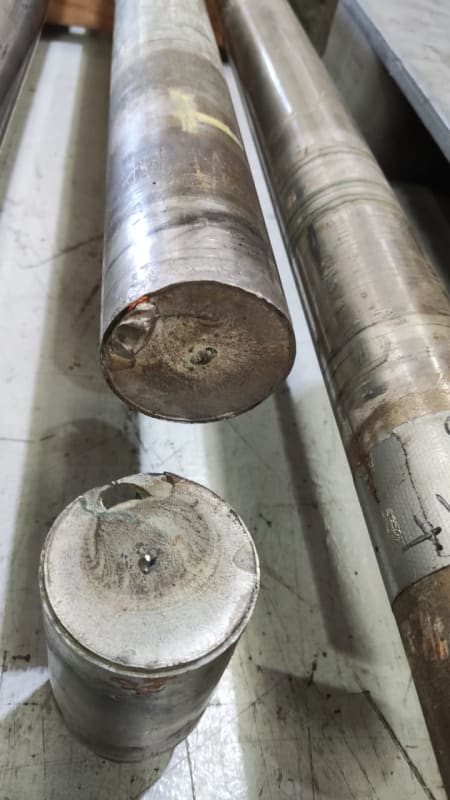
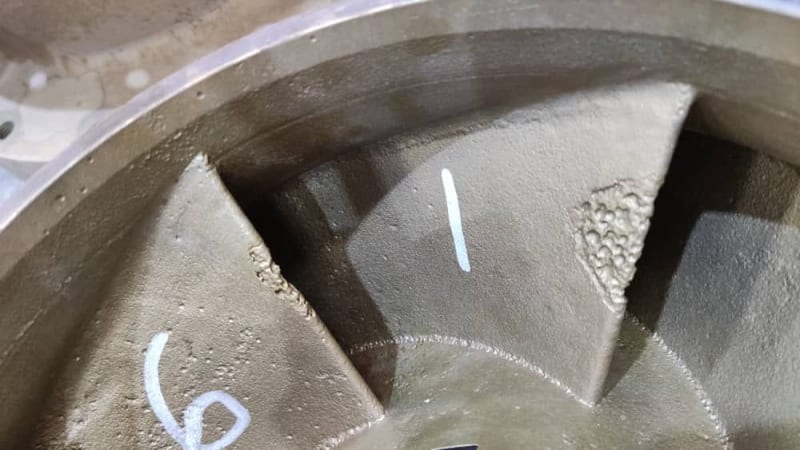
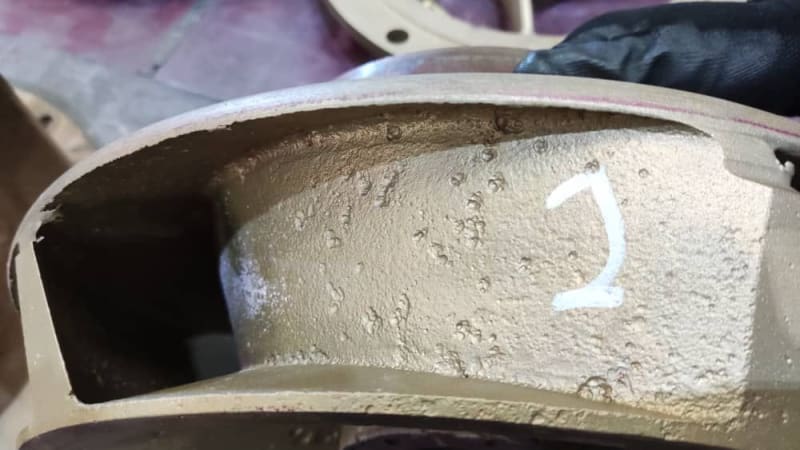
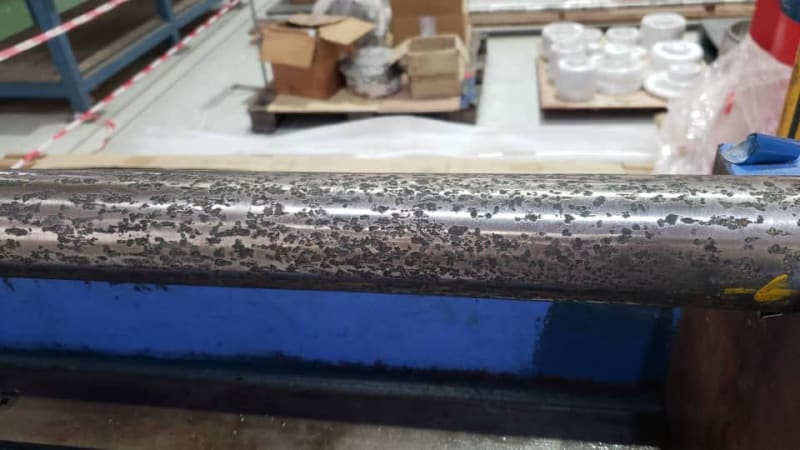
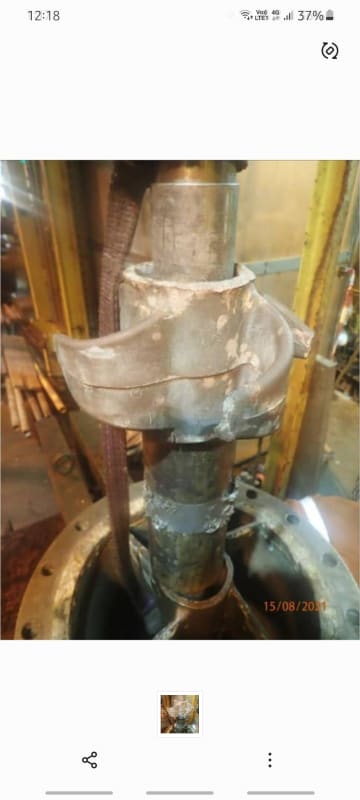