EulersBucklers
Structural
I have a column that the architect would like to walk over. Consider the top, transition and bottom columns to all be the same thickness into the page. I am in the United States so ACI 318 prevails.
I'm thinking of doing a strut and tie check in addition to some other checks and I am struggling with the strut capacity calculation. I am considering the strut in the transition column to be bottle-shaped and, per ACI, I would use a βs factor of 0.6 (without special transverse reinforcement) or 0.75 (with special transverse reinforcement). I want to reinforce the walked column conventionally with vertical steel and horizontal ties. Here is where I would like to see the forum's opinions:
1) Per ACI, I can't consider longitudinal reinforcement that isn't parallel with the strut axis in the strut capacity. This kills me if all my steel is vertical and horizontal and actually results in having less compressive capacity in the transition column as in the top column.
2) It appears to me like there should be an angle of strut inclination that should be "close enough" to parallel so that I don't have to disregard my vertical steel (maybe less than 10 degrees?). Otherwise you'd have to resort to inclined reinforcement which looks odd to me and seems unnecessary.
What does the forum think on this "close enough" idea? Maybe other codes have weighed in on this?
I'm thinking of doing a strut and tie check in addition to some other checks and I am struggling with the strut capacity calculation. I am considering the strut in the transition column to be bottle-shaped and, per ACI, I would use a βs factor of 0.6 (without special transverse reinforcement) or 0.75 (with special transverse reinforcement). I want to reinforce the walked column conventionally with vertical steel and horizontal ties. Here is where I would like to see the forum's opinions:
1) Per ACI, I can't consider longitudinal reinforcement that isn't parallel with the strut axis in the strut capacity. This kills me if all my steel is vertical and horizontal and actually results in having less compressive capacity in the transition column as in the top column.
2) It appears to me like there should be an angle of strut inclination that should be "close enough" to parallel so that I don't have to disregard my vertical steel (maybe less than 10 degrees?). Otherwise you'd have to resort to inclined reinforcement which looks odd to me and seems unnecessary.
What does the forum think on this "close enough" idea? Maybe other codes have weighed in on this?
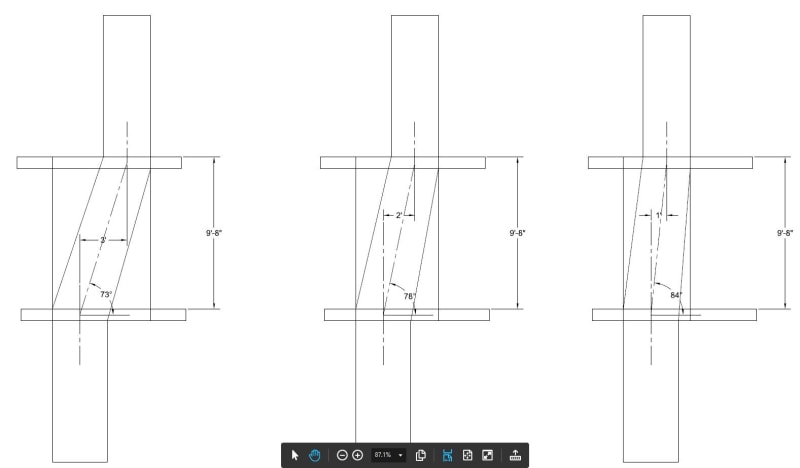