Managuensis
Automotive
Hello
We have a battery enclosure and it is mounted in its place using two locator pins at the rear face. During the vibration test named SAE J2380(Vibration Testing for EV batteries), the nut got loose and hence the pin got loose in its position which resulted in test failure. We did not observe any loosening for the twin locator pin which had a glued nut (blue Loctite). Therefore we decided to replace the plain washer with a Nord-lock washer which you can see below. The Nord-lock washer pair sits on two different surfaces. These surfaces are flush, however each has +/- 0.1 mm of tolerance. So they may not be flush afterall due to tolerance. Would Nord-lock washer work in this scenario? If not, what can be done instead?
Nord-lock washer:
We have a battery enclosure and it is mounted in its place using two locator pins at the rear face. During the vibration test named SAE J2380(Vibration Testing for EV batteries), the nut got loose and hence the pin got loose in its position which resulted in test failure. We did not observe any loosening for the twin locator pin which had a glued nut (blue Loctite). Therefore we decided to replace the plain washer with a Nord-lock washer which you can see below. The Nord-lock washer pair sits on two different surfaces. These surfaces are flush, however each has +/- 0.1 mm of tolerance. So they may not be flush afterall due to tolerance. Would Nord-lock washer work in this scenario? If not, what can be done instead?
Nord-lock washer:
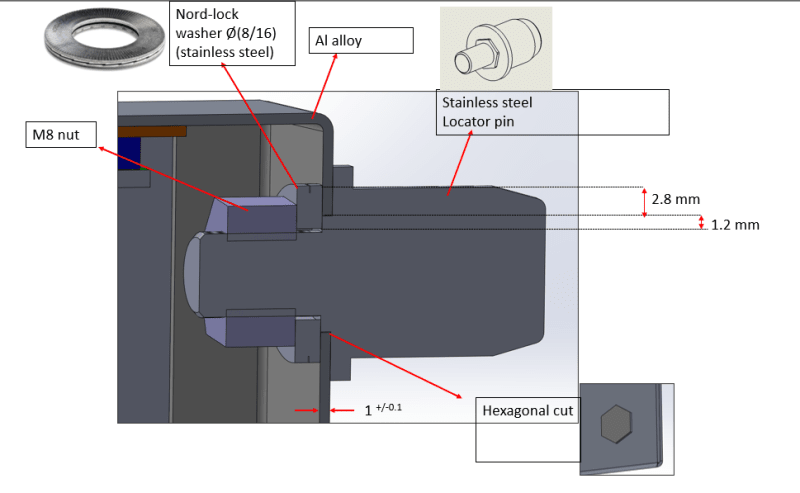