I was asked by a customer to see if I could calculate a load rating for a platform that they use while working on a piece of equipment. I have done this before on shelf or racks that we have built for him in the past but it is not really my specialty. This one has gone beyond my basic structural knowledge, they are using ubolt brackets to support the top of the platform to poles that are then set into the ground. I believe I will need to find the surface area of contacts and the force to find the friction, is there an easier way to estimate this?
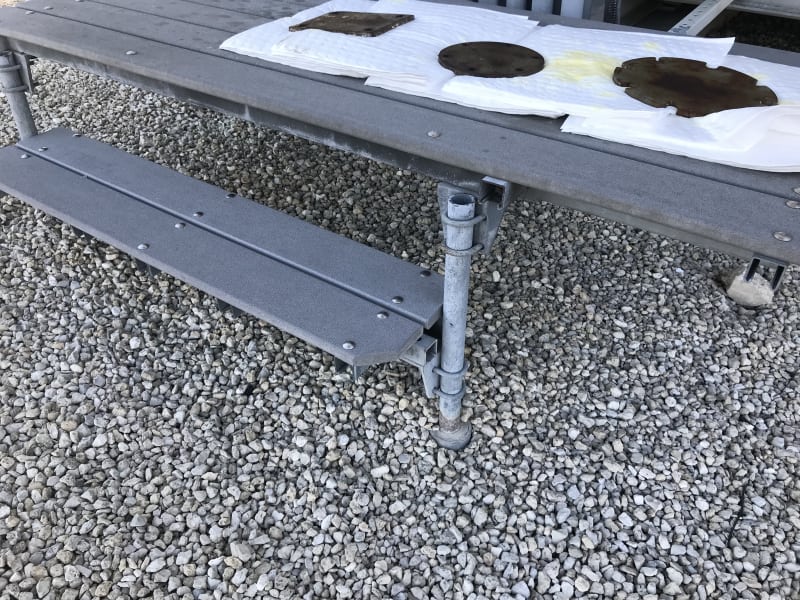