I am looking at the weld of a 5/8" diameter bar to a 3/4" bar post. Given the tolerances I know I can't get an adequate fillet weld all around. So my question is this, I am looking at Blodgett's book and his table showing the section moduli for different weld shapes. He shows the modulus for a circular weld, but is there any way that I could find the section modulus of two arcs instead of a full circle to account for no effective weld at the narrow sides of the connection? I have attached a quick sketch showing what I mean.
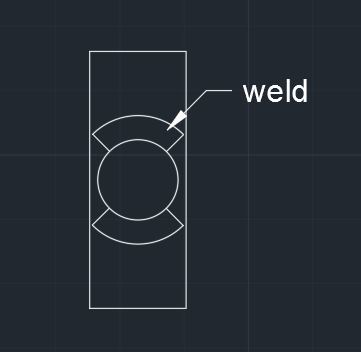