iam42
Industrial
- Feb 15, 2007
- 175
Hi Guys,
I have a job coming up that requires us to weld 3" thick SA182-347 to SA106 Gr. C Pipe. I am no metallurgist but I have read enough in here to scare me a little with regards to Re-Heat Cracking on thick sections. I am not sure if this is a major factor but the design temp for this joint is 550°F
My Plan at the moment is to butter the CS weld bevel with ERNiCr-3 and then PWHT the CS pipe. I then plan to weld the joint with ER347 in a similar manner to a standard 316 or 304 joint.
Is my plan flawed and doomed to failure?
If so, can some kind sole please suggest a better approach.
Many Thanks
I have a job coming up that requires us to weld 3" thick SA182-347 to SA106 Gr. C Pipe. I am no metallurgist but I have read enough in here to scare me a little with regards to Re-Heat Cracking on thick sections. I am not sure if this is a major factor but the design temp for this joint is 550°F
My Plan at the moment is to butter the CS weld bevel with ERNiCr-3 and then PWHT the CS pipe. I then plan to weld the joint with ER347 in a similar manner to a standard 316 or 304 joint.
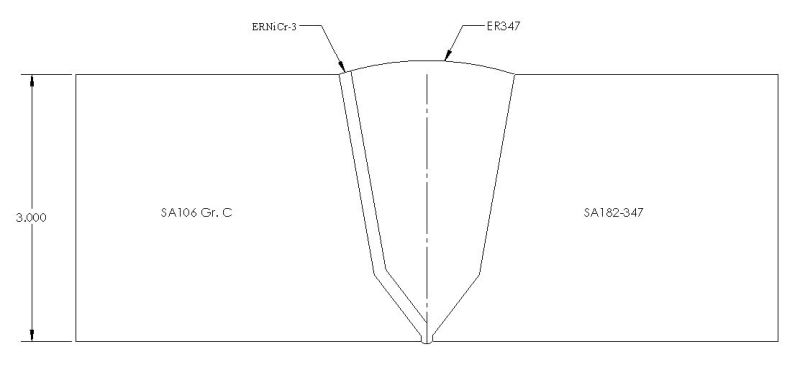
Is my plan flawed and doomed to failure?
If so, can some kind sole please suggest a better approach.
Many Thanks