Dear All,
I am looking for documentation (acceptance criteria, WPQR, ...) for the butt welding of rails using SMAW or FCAW in copper blocks (see attached pic).
I am quite familiar with the welding of rails, and know the relevant EN or EN ISO standards (e.g. for thermite and repair welding of rails, ...), however for this type of welding there is no general code.
Does someone with access to the AREMA manual knows whether this is a subject that is treated in the AREMA (or in a similar code)?
---
I am looking for documentation (acceptance criteria, WPQR, ...) for the butt welding of rails using SMAW or FCAW in copper blocks (see attached pic).
I am quite familiar with the welding of rails, and know the relevant EN or EN ISO standards (e.g. for thermite and repair welding of rails, ...), however for this type of welding there is no general code.
Does someone with access to the AREMA manual knows whether this is a subject that is treated in the AREMA (or in a similar code)?
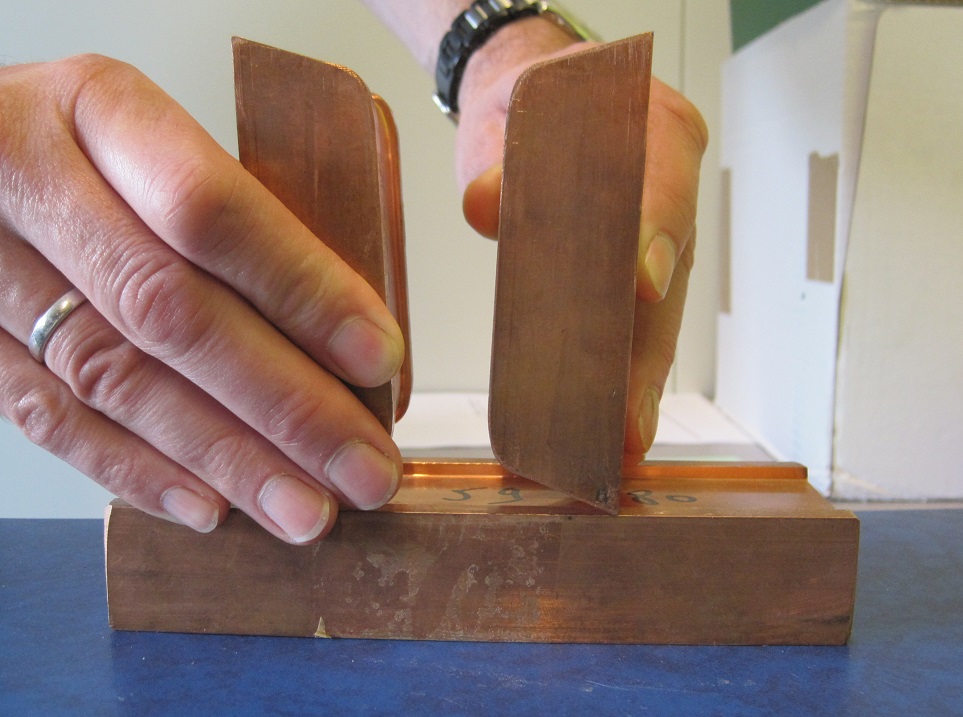
---