Hi,
Below is a picture of a recent re-weld at the base of a lug. This is an old 1950's structure with not a lot of good documentation - both the lug and the shell are thought to be mild steel. The weld was re-done by a certified structural welder after some cracking had been found. The welder ground off the old cracked weld first then applied a fresh new weld. A couple of months later the cracking returned as shown in the photo - the cracks look the same was what was originally found. There is not a lot of axial load on the lug, there is some cyclic bending at the base of the lug which could imply a fatigue crack - but it does not seem to look like a fatigue crack. It is very straight and sharp and transitions seamlessly from the weld metal to the base metal. Any thoughts or ideas?
The interface does not see low temperatures. The structure is located indoors and is maintained between 15 and 25 degrees celcius.
Thanks,
22west
Below is a picture of a recent re-weld at the base of a lug. This is an old 1950's structure with not a lot of good documentation - both the lug and the shell are thought to be mild steel. The weld was re-done by a certified structural welder after some cracking had been found. The welder ground off the old cracked weld first then applied a fresh new weld. A couple of months later the cracking returned as shown in the photo - the cracks look the same was what was originally found. There is not a lot of axial load on the lug, there is some cyclic bending at the base of the lug which could imply a fatigue crack - but it does not seem to look like a fatigue crack. It is very straight and sharp and transitions seamlessly from the weld metal to the base metal. Any thoughts or ideas?
The interface does not see low temperatures. The structure is located indoors and is maintained between 15 and 25 degrees celcius.
Thanks,
22west
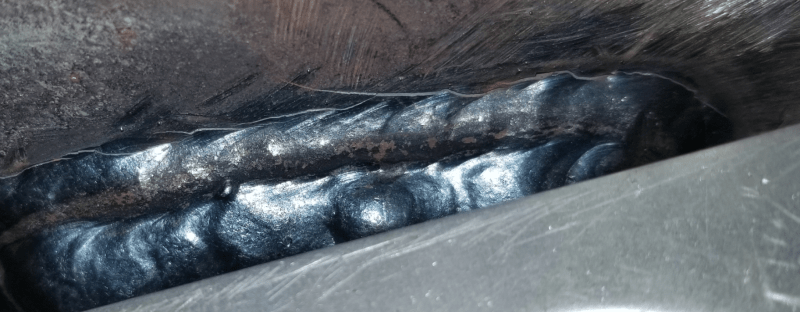