-
1
- #1
rebarfixer.hk
Structural
- Aug 16, 2022
- 4
hi there, i am new to this industry and this forum, but i encountered some problem and it seems eng-tip is the only forum that can answer my question.
So, in the general notes of the site that i am working with, there is a typical anchorage detail of slab says that the top bar of slab can be straight as long as it has a full anchorage length to beam.
but unfortunately, there are hooks in every single slab drawing, especially to beam that is located at the edge of building.
The length of hooks were not specified, and it seems to me that it is just merely illustration but not a construction requirement. However some people disagreed...
So, is it a must to have slab top bar hooked down?
whats the different between straight bar and hooked bar given that they both have sufficient length to fulfill the anchorage requirement?
sorry for my poor english and thank you very much for your time![[smile] [smile] [smile]](/data/assets/smilies/smile.gif)
So, in the general notes of the site that i am working with, there is a typical anchorage detail of slab says that the top bar of slab can be straight as long as it has a full anchorage length to beam.
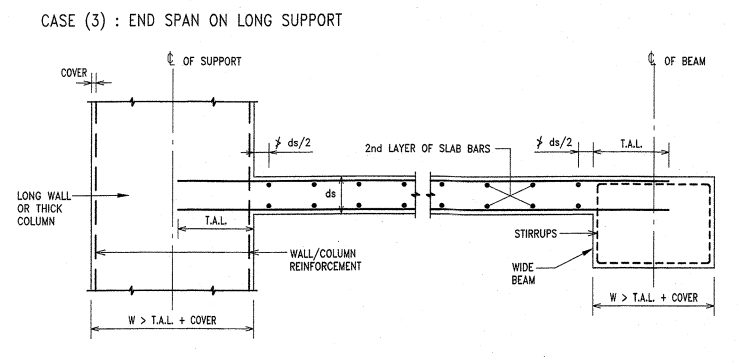
but unfortunately, there are hooks in every single slab drawing, especially to beam that is located at the edge of building.
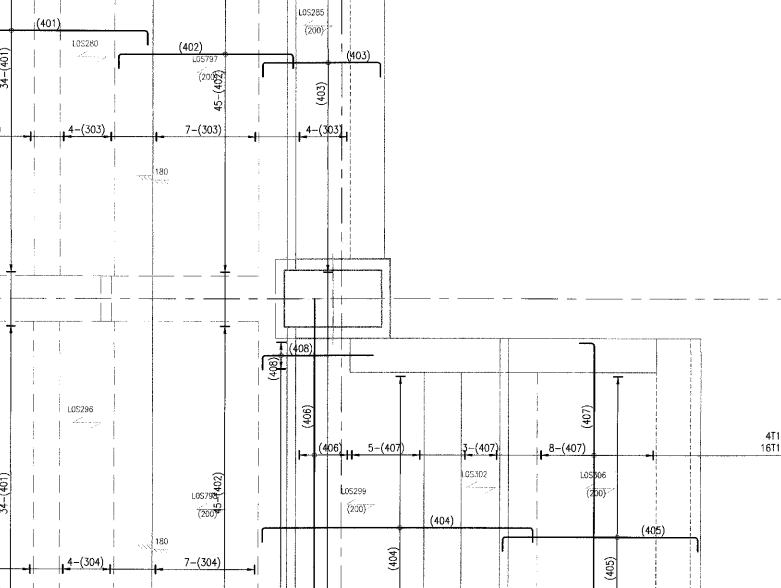
The length of hooks were not specified, and it seems to me that it is just merely illustration but not a construction requirement. However some people disagreed...
So, is it a must to have slab top bar hooked down?
whats the different between straight bar and hooked bar given that they both have sufficient length to fulfill the anchorage requirement?
sorry for my poor english and thank you very much for your time
![[smile] [smile] [smile]](/data/assets/smilies/smile.gif)