cicciobaruffi
Electrical
Hello,
I need to build a test instrumentation for a customer and I would like to ask your feedback regarding the best motor type to be used.
The system will be made like this:
The goal is to actuate a torque profile in a way that the force acted on the rope by the device is opposed.
The requirements are:
1- The control needs to be with torque set point (I need to create a torque profile)
2- The torque required ON THE MOTOR is from 1Nm to 4 Nm and I can not decrease it adapting the mechanical transmission
3- The motor will actuate this torque very often with 0 speed
4- The power supply will be 230 VAC 1-phase and, if required, I can use a Vac-Vdc converter
5- The cost of the equiment must be as low as possible
If I didn’t have any cost costraints my choice would be AC brushless motor + servo drive and by this solution I could satisfy all the requirements but, unfortunately, it is absolutely too expensive for the customer.
So I am searching for cheaper solution. I searched for DC motors and AC motors but I don’t have a lot of experience with this kind of motors and I ask your help.
Can you please give me your feedback about it?
Please write me if something is not clear and thanks in advance!
Thanks!
I need to build a test instrumentation for a customer and I would like to ask your feedback regarding the best motor type to be used.
The system will be made like this:
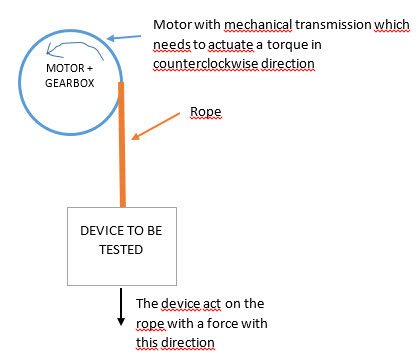
The goal is to actuate a torque profile in a way that the force acted on the rope by the device is opposed.
The requirements are:
1- The control needs to be with torque set point (I need to create a torque profile)
2- The torque required ON THE MOTOR is from 1Nm to 4 Nm and I can not decrease it adapting the mechanical transmission
3- The motor will actuate this torque very often with 0 speed
4- The power supply will be 230 VAC 1-phase and, if required, I can use a Vac-Vdc converter
5- The cost of the equiment must be as low as possible
If I didn’t have any cost costraints my choice would be AC brushless motor + servo drive and by this solution I could satisfy all the requirements but, unfortunately, it is absolutely too expensive for the customer.
So I am searching for cheaper solution. I searched for DC motors and AC motors but I don’t have a lot of experience with this kind of motors and I ask your help.
Can you please give me your feedback about it?
Please write me if something is not clear and thanks in advance!
Thanks!
