Hi all
As you see in this following photo which is the driving system for a bottle filling machine, there's a set of gears run by an electromotor, that end up to a pully timing belt system that provides the machine position read for an encoder. my question is: if there are two or three gear to gear contacts before this pully, that can have an error. but when we get to the encoder we use belt to increase the rotating precision ? I feel something is missing or I don't know
As you see in this following photo which is the driving system for a bottle filling machine, there's a set of gears run by an electromotor, that end up to a pully timing belt system that provides the machine position read for an encoder. my question is: if there are two or three gear to gear contacts before this pully, that can have an error. but when we get to the encoder we use belt to increase the rotating precision ? I feel something is missing or I don't know
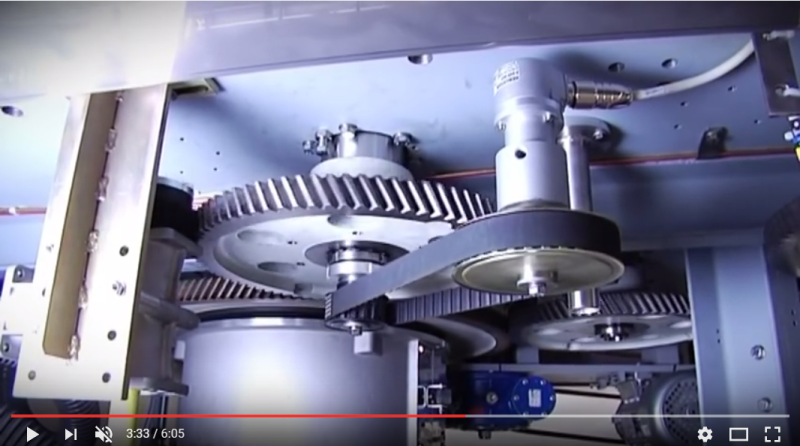