milkshakelake
Structural
Need help with two details. Feel free to mercilessly tear them apart. My concerns:
1. For the interior bearing wall, I'm putting 3 pieces of solid blocking. I'm wondering if it's necessary. I want to transfer shear wall loads from the shear wall above. This detail occurs in 30ish places and these walls are 4 stories high, so I want to reduce solid blocking for cost. The other reason is for stud wall bearing. But maybe a single piece of solid blocking in the middle (for non-shear walls) and 2 pieces of solid blocking (only at shear walls, not the whole length of the wall) would be enough. Also concerned about eccentric loading if I use 2 pieces of solid blocking, but like my exterior wall detail, I think it's pretty common practice.
2. For the exterior bearing wall, I'm using the top plates as the collector/drag strut with 2500# force. I'm wondering if a rim truss is capable of transferring the load from the sill plate to the top plate, and if I'm missing something in the load path. And if I need shear clips, like Simpson LTP4.
1. For the interior bearing wall, I'm putting 3 pieces of solid blocking. I'm wondering if it's necessary. I want to transfer shear wall loads from the shear wall above. This detail occurs in 30ish places and these walls are 4 stories high, so I want to reduce solid blocking for cost. The other reason is for stud wall bearing. But maybe a single piece of solid blocking in the middle (for non-shear walls) and 2 pieces of solid blocking (only at shear walls, not the whole length of the wall) would be enough. Also concerned about eccentric loading if I use 2 pieces of solid blocking, but like my exterior wall detail, I think it's pretty common practice.
2. For the exterior bearing wall, I'm using the top plates as the collector/drag strut with 2500# force. I'm wondering if a rim truss is capable of transferring the load from the sill plate to the top plate, and if I'm missing something in the load path. And if I need shear clips, like Simpson LTP4.
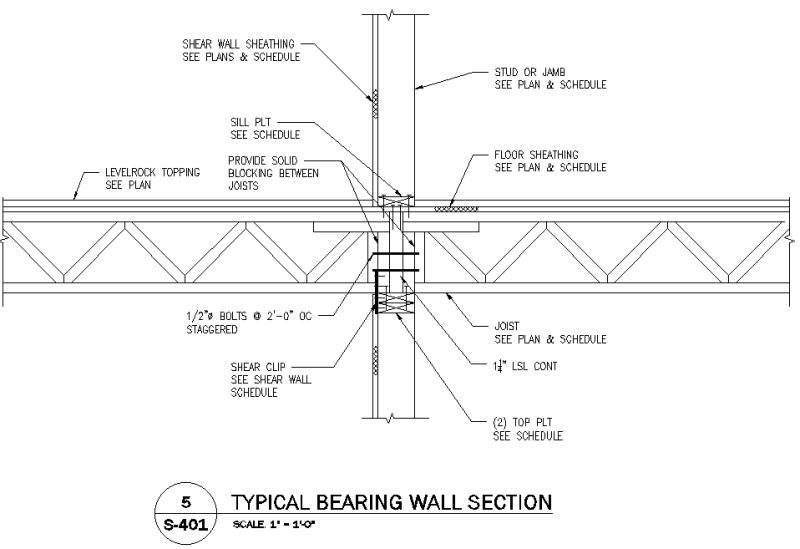
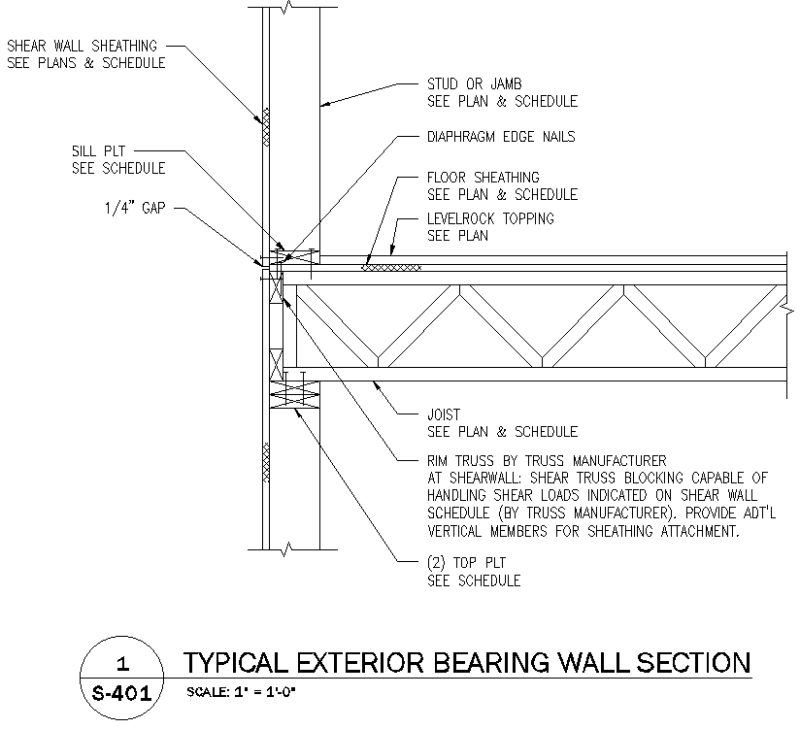