thejonster
Structural
- Feb 8, 2011
- 69
With wood purlins, I'm discovering that I have to resist rolling, this due to the lateral component of the purlin reaction on a sloped roof and the distance from the centroid of the purlin to the bearing point. This is significant because the reaction force, normally taken in bearing is large compared to what I can use to resist it.
Normally "Compression perpendicular to grain" (Fc⫠) is used for wood connections in bearing (~3.3k per 2x6 area), but on a 6:12 sloped truss, I have to use nails or screws to 'bear' the reaction against sliding (only ~110 to 170lb per toe screw depending on Cd of load case), you can see how this would add up. I'm using screws because nails are so terrible in withdrawal, and uplift is a factor. I usually see flat purlins for this reason, but I'm using upright purlins because customer requires 10' spacing for some nice glulam trusses.
My main question: (if TL;DR)
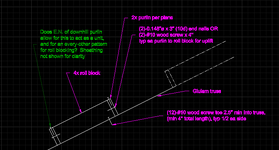
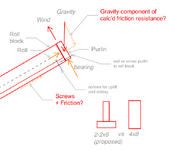
Normally "Compression perpendicular to grain" (Fc⫠) is used for wood connections in bearing (~3.3k per 2x6 area), but on a 6:12 sloped truss, I have to use nails or screws to 'bear' the reaction against sliding (only ~110 to 170lb per toe screw depending on Cd of load case), you can see how this would add up. I'm using screws because nails are so terrible in withdrawal, and uplift is a factor. I usually see flat purlins for this reason, but I'm using upright purlins because customer requires 10' spacing for some nice glulam trusses.
My main question: (if TL;DR)
- is wood to wood friction component allowed in calculation to reduce the amount of screws needed to resist sliding down the truss? A search of the NDS for 'friction' returns nothing. This is a large roof the saving would be huge, reducing screws needed by half (adding up to thousands on this roof).
- Does anyone else have a better way of doing this? This is my first attempt at this problem, and using 4x6 purlins would mean almost 2x overall greater wood mass, or using a steel angle w/ 2x8 requires L8x__x1/4" and some prying calcs. Or does Simpson make a product for purlin roll & sliding?
- Does edge nailing of downhill purlin allow for this to act as a unit, and allow for an 'every-other' pattern for roll blocking? Sheathing not shown for clarity.
- Please confirm? I believe it's appropriate to use the full bearing component of gravity load for the friction calculation. Even when lubricated, wood-wood has a .20 coeff of friction. re: https://www.engineersedge.com/coeffients_of_friction.htm .. I'd rather use a value published from AWS, but sadly did not find.
- I think I've answered this question, but: customer proposed 2x6 assembly, but I think 4x8 best: making an assembly requires more nails and labor (and calcs), and leaves a 1/2" gap at top, doesn't save much wood.
- Bonus: Use 20' purlins and stagger layout?
- Also: NDS 2018 11.3.1 says wood screws are subject to toe-nail factor in shear and withdrawal.. so I'm detailing a toe 'nailed' wood screw and using the .83 & .67 Ctn factors respectively. I just think it's oddly named for screws & bolts, first time realizing it applies to those.
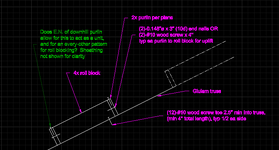
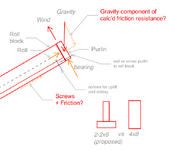
Attachments
Last edited: