Hi all,
I have a question relating to hydraulic logic, I think that's the right way of phrasing it.
I am planning to connect hydraulic cylinders in a fixed volume system based below. At the moment I am considering it as an ideal system, fluid not compressible, not considering temp changes etc.
Here is a diagram of the system:
Cylinders one and two are connected to front and rear axles of a car respectively. I am considering the car to have an uneven F:R weight distribution, hence unequal forces (120:100N). The fluid from both cylinders will be displaced into cylinder 3 when the static weight of the car is fed through pistons 1 and 2. I need to know the force that will act at piston 3 with a specified area, so I can add a spring into cylinder 3 (bounce spring) and specify it's rate to calculate the strokes of pistons 1 and 2.The problem I have is this:
If I specify the areas of pistons 1 and 2 to be the same (A1), surely with different forces there would be different pressures if the cylinders were not connected?
But as they are connected, I know the pressure must be equal, but what effect would this have on the system, and how would I calculate it?
I estimate that the forces must equalise somehow, but I don't know how I would calculate it, or if this is even correct.
I understand the basics of hydraulic leverage in a one input cylinder-one output cylinder system, but am struggling to apply that logic to this system. I plan to model this mathematically using SimHydraulics but I've never used Simulink before so it will take some time before I can try that.
If anyone could share some wisdom I would be most gratfeul.
I have a question relating to hydraulic logic, I think that's the right way of phrasing it.
I am planning to connect hydraulic cylinders in a fixed volume system based below. At the moment I am considering it as an ideal system, fluid not compressible, not considering temp changes etc.
Here is a diagram of the system:
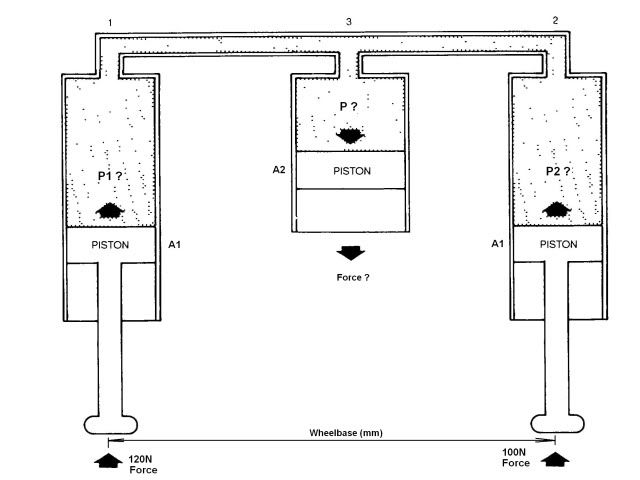
Cylinders one and two are connected to front and rear axles of a car respectively. I am considering the car to have an uneven F:R weight distribution, hence unequal forces (120:100N). The fluid from both cylinders will be displaced into cylinder 3 when the static weight of the car is fed through pistons 1 and 2. I need to know the force that will act at piston 3 with a specified area, so I can add a spring into cylinder 3 (bounce spring) and specify it's rate to calculate the strokes of pistons 1 and 2.The problem I have is this:
If I specify the areas of pistons 1 and 2 to be the same (A1), surely with different forces there would be different pressures if the cylinders were not connected?
But as they are connected, I know the pressure must be equal, but what effect would this have on the system, and how would I calculate it?
I estimate that the forces must equalise somehow, but I don't know how I would calculate it, or if this is even correct.
I understand the basics of hydraulic leverage in a one input cylinder-one output cylinder system, but am struggling to apply that logic to this system. I plan to model this mathematically using SimHydraulics but I've never used Simulink before so it will take some time before I can try that.
If anyone could share some wisdom I would be most gratfeul.