Full disclosure: The device in question is more hobby than work related. But as engineers, safety is paramount is all aspects of our lives. Since my question is safety related, and I'm thinking of making a report to the relevant government agency, I believe my question should be allowed.
Please see the connection between the threaded rod and collar in the photo. The threads don't end at the bottom of the collar, but extend to the top of the rod above the pin connection. The inside of the collar is cylindrical, not threaded. This means the pin crosses a bit of a gap, unlike the upper pin which joins a cylindrical shaft and hole. I believe the gap causes some of the stress on the pin to be bending moment instead of straight shear like in the upper pin. Is this EE correct on this mechanical issue? Is this a proper application? I had a pin like this one (not my photo) fail at a time when it caused no safety issue, but at another time it might have caused a motor vehicle accident. Thanks.
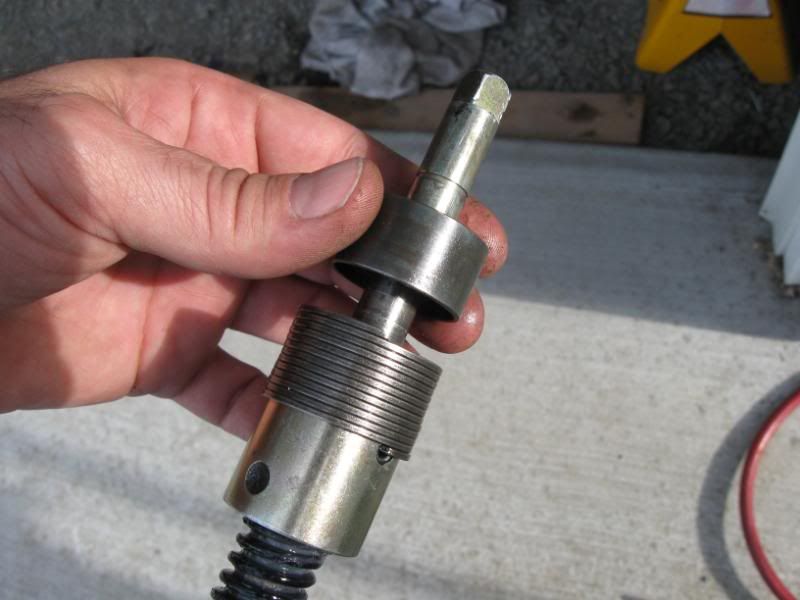
Please see the connection between the threaded rod and collar in the photo. The threads don't end at the bottom of the collar, but extend to the top of the rod above the pin connection. The inside of the collar is cylindrical, not threaded. This means the pin crosses a bit of a gap, unlike the upper pin which joins a cylindrical shaft and hole. I believe the gap causes some of the stress on the pin to be bending moment instead of straight shear like in the upper pin. Is this EE correct on this mechanical issue? Is this a proper application? I had a pin like this one (not my photo) fail at a time when it caused no safety issue, but at another time it might have caused a motor vehicle accident. Thanks.