Guastavino
Structural
Hi All,
I got called out to a building that is about 35 years old where there are mortar joint cracks at about 16" o/c (see attached picture). The spacing coincides with the locations of the horizontal joint reinforcing. It's a 4" Brick, 8" block wall. As you can see in the picture the joint reinforcing has corroded.
My thoughts are the masonry ladder reinforcing has corroded (which you can see in the picture), thus expanded, and cracked the mortar joints over time. Then possibly freeze/thaw too.
My repair/recommendation would be to remove the damaged ladder reinforcing from the mortar joint and provide retrofit brick ties to anchor the veneer back to the CMU backing and tuckpoint the wall.
My question is does anyone else have any reason to think I'm off? Is there something I could be missing you all can think of? I think this is simple diagnosis, but it almost feels too simple.
Thanks!
Nick
I got called out to a building that is about 35 years old where there are mortar joint cracks at about 16" o/c (see attached picture). The spacing coincides with the locations of the horizontal joint reinforcing. It's a 4" Brick, 8" block wall. As you can see in the picture the joint reinforcing has corroded.
My thoughts are the masonry ladder reinforcing has corroded (which you can see in the picture), thus expanded, and cracked the mortar joints over time. Then possibly freeze/thaw too.
My repair/recommendation would be to remove the damaged ladder reinforcing from the mortar joint and provide retrofit brick ties to anchor the veneer back to the CMU backing and tuckpoint the wall.
My question is does anyone else have any reason to think I'm off? Is there something I could be missing you all can think of? I think this is simple diagnosis, but it almost feels too simple.
Thanks!
Nick
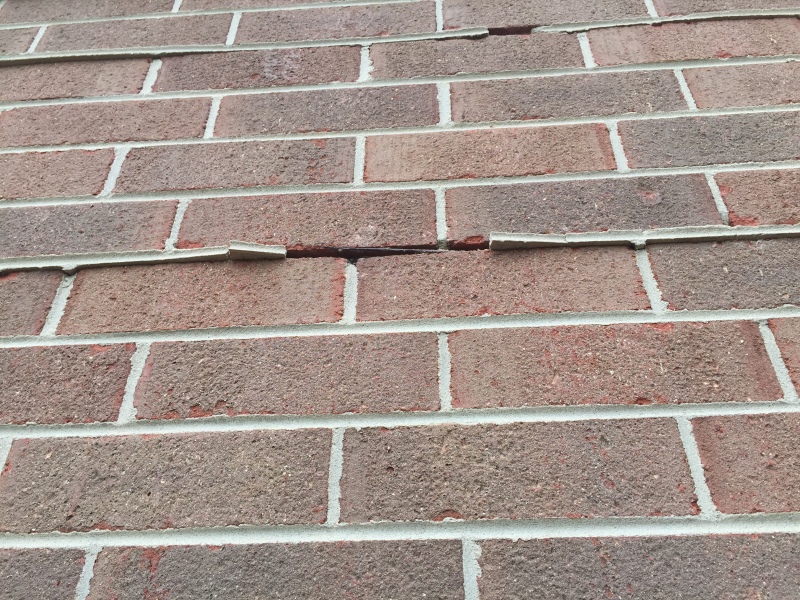