bootlegend
Structural
I have a situation where a 10" industrial walkway channel needs to be cut to allow head clearance for a walkway below. I think I have a relatively simple solution of welding a plate across the bottom as shown below to create a box type section. Yielding of the section should be no issue but I want to make sure the top plate doesn't have a buckling issue under compression due to bending. I used the AISC equations for bending in unsymmetrical members and used the critical buckling stress for a flat plate under compression as the Fcr in the AISC equations. I know the AISC equations are asking for the Fcr of the whole section, but the top plate would buckle first and so seems conservative to simply use the plate buckling stress.
My question is does this approach seem reasonable or is there some other more appropriate method I should use? By the way, I realize now that I should use the full width of the plate for the b value so that will result in a lower Fcr than shown.
My question is does this approach seem reasonable or is there some other more appropriate method I should use? By the way, I realize now that I should use the full width of the plate for the b value so that will result in a lower Fcr than shown.
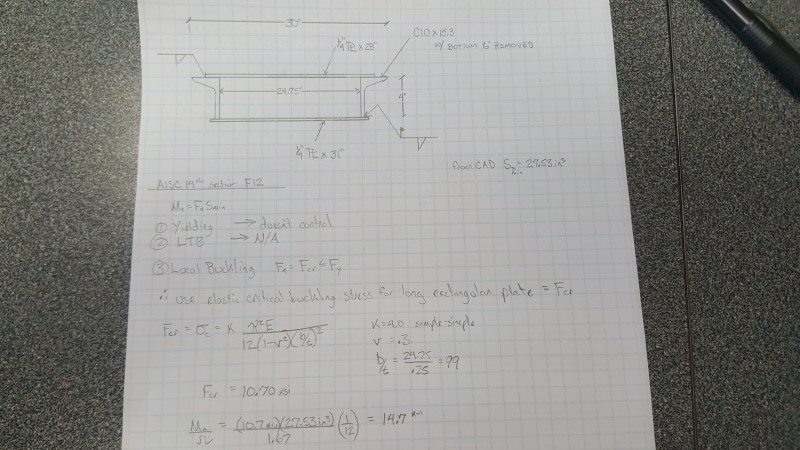