MasterrrrBlasterrrr
Structural
thread507-434905
My calculation for the baseplate capacity in the thread I have referenced:
(1) Calculate the bolt tension. I would use the lever arm from web of the 50SHS to the line of bolts.
e = 25 - 2.5 = 22.5mm (assuming 5mm wall)
M* = 3.2 x 0.4 = 1.28 kNm
T*b = 1.28/(0.0225x2) = 28.4 kN
(Check the nominated chemset anchor has this capacity)
(2) Check bending of the plate.
I'm assuming the bolt is 50mm from the face of SHS
For simplicity, will first assume the plate cantilevers from the SHS.
M*plate = 28.4*0.05 = 1.42 kNm
There is 100mm width of plate to act as a cantilever.
Sx = 100x10^2/4 = 2500 mm^3
Fb = M/S = 1.42E6/2500 = 568 MPa.
FAILS.
Using Yield Lines, the effective length of plate that yields = 2x100 + 85.
The bending stress over a yield line length of 285mm = 199 MPa.
This is acceptable, but highly stressed.
I would make the dropper larger, and the plate wider and thicker.
Would prefer a design solution where the plate is OK in one-way bending as a cantilever.
The yield line pattern that accompanies the 285mm length probably involves prying action on the bolt?
So, the bolt tension may be 30% or so greater than 28.4 kN.
I suggest a 75SHS dropper, with 150x12 plate.
T*b = 1.28/(0.035*2) = 18.3 kN
M*plate = 18.3 x 0.05 = 0.91 kNm (assuming one way bending in cantilever action)
Sx =150x12^2/4= 5400 mm^3
Fb = 0.91e6/5400 = 168 MPa
Works fine
Yield line pattern for 2 way bending in plate is attached.
In a late correction:
The portion of the yield line that has effective length 85mm undergoes rotation of "2 theta".
If doing calcs by virtual work, the M*theta for this component will be 2 x 85 = 170mm
So, total effective length of yield line that unrgoes "1xtheta" rotation = 370mm
My calculation for the baseplate capacity in the thread I have referenced:
(1) Calculate the bolt tension. I would use the lever arm from web of the 50SHS to the line of bolts.
e = 25 - 2.5 = 22.5mm (assuming 5mm wall)
M* = 3.2 x 0.4 = 1.28 kNm
T*b = 1.28/(0.0225x2) = 28.4 kN
(Check the nominated chemset anchor has this capacity)
(2) Check bending of the plate.
I'm assuming the bolt is 50mm from the face of SHS
For simplicity, will first assume the plate cantilevers from the SHS.
M*plate = 28.4*0.05 = 1.42 kNm
There is 100mm width of plate to act as a cantilever.
Sx = 100x10^2/4 = 2500 mm^3
Fb = M/S = 1.42E6/2500 = 568 MPa.
FAILS.
Using Yield Lines, the effective length of plate that yields = 2x100 + 85.
The bending stress over a yield line length of 285mm = 199 MPa.
This is acceptable, but highly stressed.
I would make the dropper larger, and the plate wider and thicker.
Would prefer a design solution where the plate is OK in one-way bending as a cantilever.
The yield line pattern that accompanies the 285mm length probably involves prying action on the bolt?
So, the bolt tension may be 30% or so greater than 28.4 kN.
I suggest a 75SHS dropper, with 150x12 plate.
T*b = 1.28/(0.035*2) = 18.3 kN
M*plate = 18.3 x 0.05 = 0.91 kNm (assuming one way bending in cantilever action)
Sx =150x12^2/4= 5400 mm^3
Fb = 0.91e6/5400 = 168 MPa
Works fine
Yield line pattern for 2 way bending in plate is attached.
In a late correction:
The portion of the yield line that has effective length 85mm undergoes rotation of "2 theta".
If doing calcs by virtual work, the M*theta for this component will be 2 x 85 = 170mm
So, total effective length of yield line that unrgoes "1xtheta" rotation = 370mm
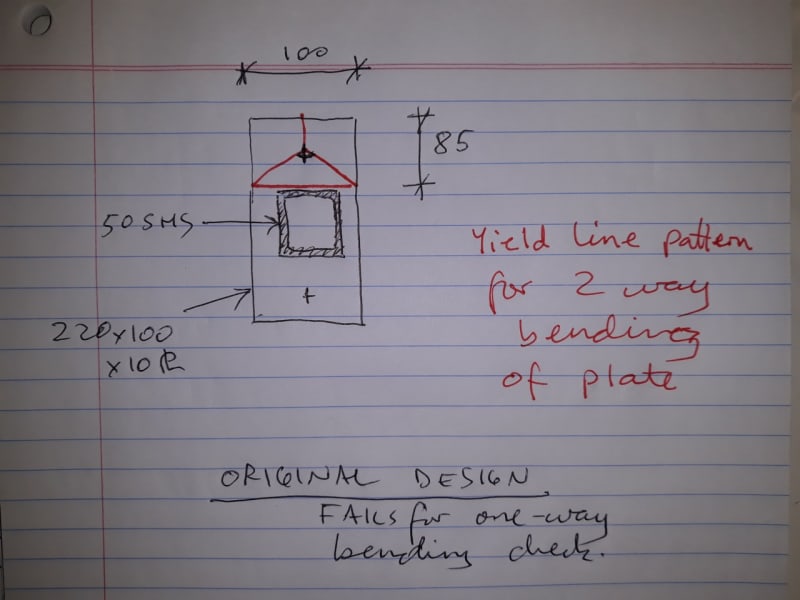