RD2EN
Structural
- Oct 25, 2019
- 12
Below is the screenshot of a basement I did and I have done some simplified hand calculation on the bored piers design by making the left hand side 'capping beam - shotcrete wall' straight instead of offset as shown and then when I use FEA analysis I realise that the reactions at the corner differ greatly from my simplified computation! (capping beams are assigned with pin restraints)
The above are the results that FEA gives me. As you can see, corner point 29 & 34 has way higher reactions than others and point 30 and 33 are in tension.
Below illustrates what my simplified computation was based on.
Can anyone tell me why is that so and what to do if I already designed it as simplified method by making it straight and they already start the construction? (I didn't use FEA back then)
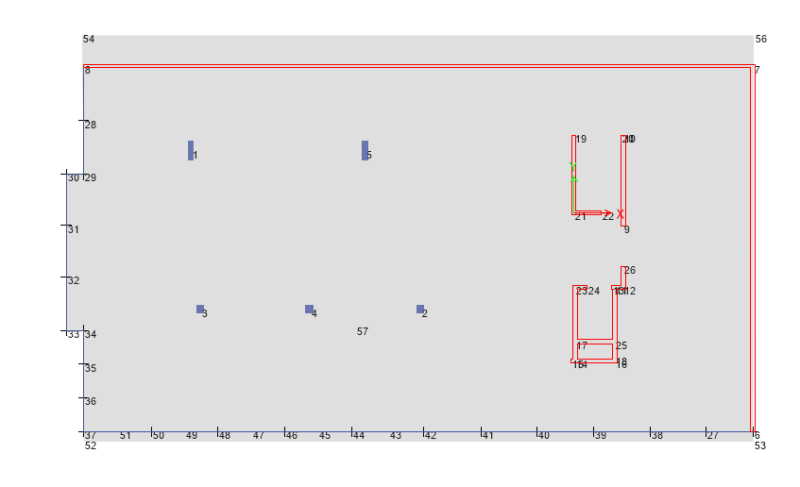
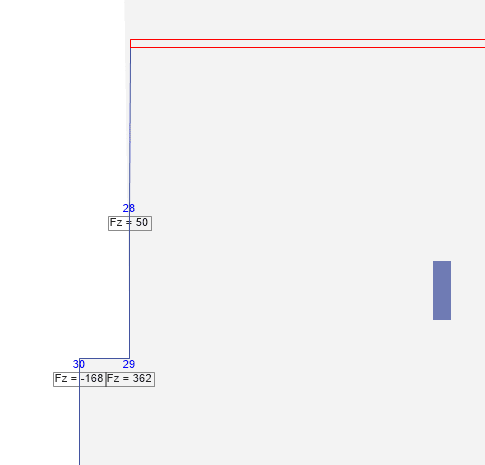
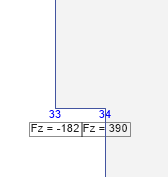
The above are the results that FEA gives me. As you can see, corner point 29 & 34 has way higher reactions than others and point 30 and 33 are in tension.
Below illustrates what my simplified computation was based on.

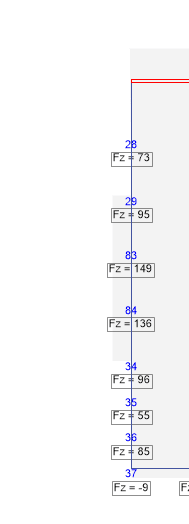
Can anyone tell me why is that so and what to do if I already designed it as simplified method by making it straight and they already start the construction? (I didn't use FEA back then)