My understanding of CMM measurements (done mostly in agreement with ISO) is limited, so I would like to ask some questions for clarification. Pretend you have a PERPENDICULARITY callout Ø0.05 to datum feature A.
When the CMM is qualifying this cylinder’s perpendicularity how this process is happening?
Let’s say 3 circles are scanned, one circle on the top of the cylinder, one in the middle and one toward the bottom. Those circles are imperfect. From each of those circles a fitted algorithm is used to generate a perfect circle, correct?
Q1: What is by default (if any) the such said algorithm? Total least squares, TLSQ? I am pretty sure the answer is TLSQ.
Then the center of this associated circle is found. Based on the fact 3 sections are measured then consequently we get 3 points/ centers which determine the extracted median line. If this imperfect line. Then, probably the software is trying to fit the smallest cylinder, perfectly perpendicular to datum A, that encompass those 3 center points. If the size of this cylinder is smaller than the TZ (tolerance zone) then the perpendicularity is qualified/ acceptable.
Here comes the essence of my thread:
Q2: If perpendicularity is called at MMC then how this TZ is calculated and also what is the relationship between measured value of the associated cylinder and the MMVC?
In other words, how a CMM knows to measure the global size (seen in blue, unrelated actual mating envelope to use ASME’s term) needed to determine the TZ size value versus to measure red size (related actual mating envelope to use ASME’s terms) needed to compare it with MMVC?
I do not think the feature (cylindrical external feature) is needed to be measured twice, just some algorithm changes are needed.
Could someone explain in detail how this procedure is done on a CMM?
When the CMM is qualifying this cylinder’s perpendicularity how this process is happening?
Let’s say 3 circles are scanned, one circle on the top of the cylinder, one in the middle and one toward the bottom. Those circles are imperfect. From each of those circles a fitted algorithm is used to generate a perfect circle, correct?
Q1: What is by default (if any) the such said algorithm? Total least squares, TLSQ? I am pretty sure the answer is TLSQ.
Then the center of this associated circle is found. Based on the fact 3 sections are measured then consequently we get 3 points/ centers which determine the extracted median line. If this imperfect line. Then, probably the software is trying to fit the smallest cylinder, perfectly perpendicular to datum A, that encompass those 3 center points. If the size of this cylinder is smaller than the TZ (tolerance zone) then the perpendicularity is qualified/ acceptable.
Here comes the essence of my thread:
Q2: If perpendicularity is called at MMC then how this TZ is calculated and also what is the relationship between measured value of the associated cylinder and the MMVC?
In other words, how a CMM knows to measure the global size (seen in blue, unrelated actual mating envelope to use ASME’s term) needed to determine the TZ size value versus to measure red size (related actual mating envelope to use ASME’s terms) needed to compare it with MMVC?
I do not think the feature (cylindrical external feature) is needed to be measured twice, just some algorithm changes are needed.
Could someone explain in detail how this procedure is done on a CMM?
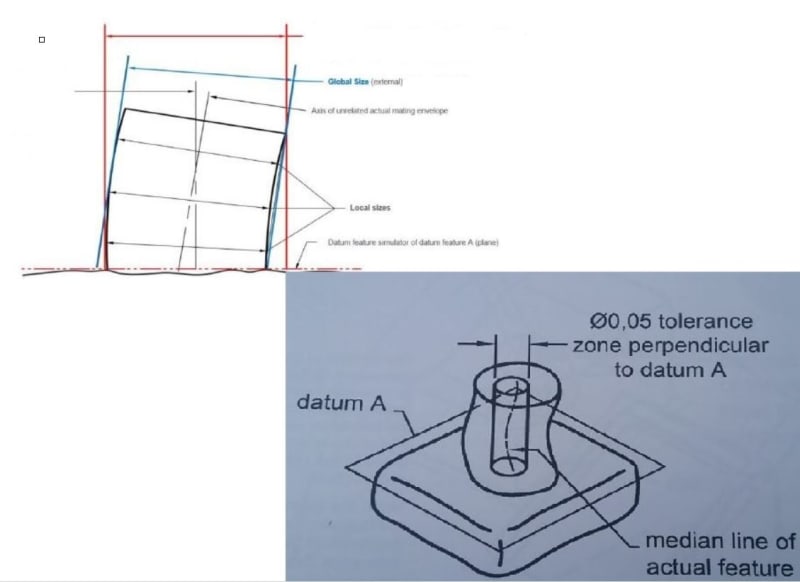