Dear All,
Im looking at a column transition head design, where the column of the structure will be directly supported on the monopile head.
Can any one please advise any "watch out" other than the direct punching shear check at column face and ecc momment due for construction tolerance?
My concern is, the dimension of the pile head will be less than 2D (code suggested critical shear perimeter), where D is depth of pile head.
many thanks upfront.
Im looking at a column transition head design, where the column of the structure will be directly supported on the monopile head.
Can any one please advise any "watch out" other than the direct punching shear check at column face and ecc momment due for construction tolerance?
My concern is, the dimension of the pile head will be less than 2D (code suggested critical shear perimeter), where D is depth of pile head.
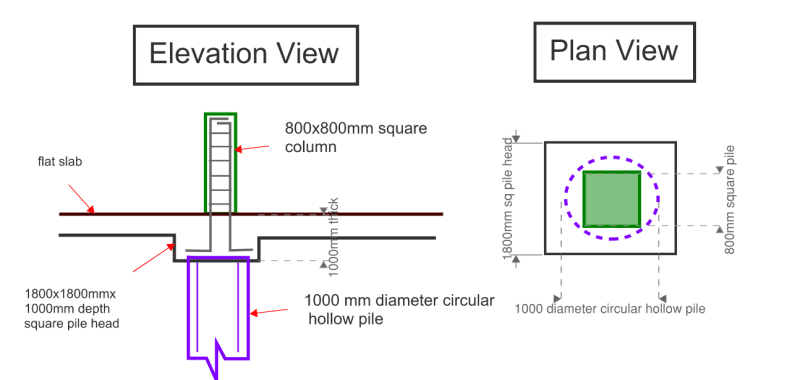
many thanks upfront.