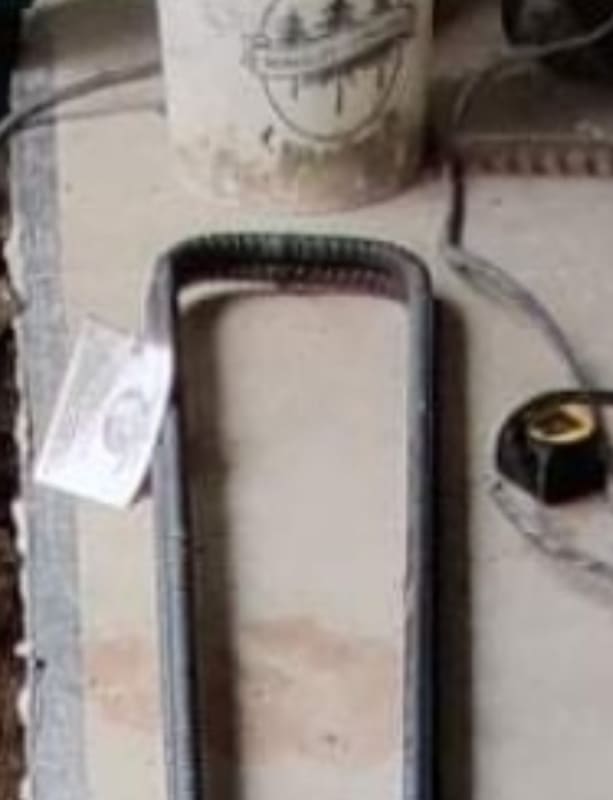
Rebar fabricator is saying I need a minimum inside dimension of 10 1/2" (2x the corner bend diameter) for a set of #7 hairpins with 90 degree bends at the belly. I'm trying to understand why they're saying that.
Any pointers? Similar bars shown in pic.
thanks
kevin