bugbus
Structural
- Aug 14, 2018
- 505
How long does a tapped hole need to be to develop the full strength of a bolt?
Below is a detail for a steel bridge bearing with tapped holes in the attachment plates. The length of the tapped holes appear to be about the same length or even slightly shorter than the bolt diameters. These bolts are subject mainly to shear force, with some tension. These are high strength bolts, Grade 8.8 (830 MPa / 120 ksi).
Does this change if we are considering Grade 4.6 (400 MPa / 58 ksi) or Grade 8.8 (830 MPa / 120 ksi) bolts?
Does it also change if the bolts are mainly in tension or shear?
Below is a detail for a steel bridge bearing with tapped holes in the attachment plates. The length of the tapped holes appear to be about the same length or even slightly shorter than the bolt diameters. These bolts are subject mainly to shear force, with some tension. These are high strength bolts, Grade 8.8 (830 MPa / 120 ksi).
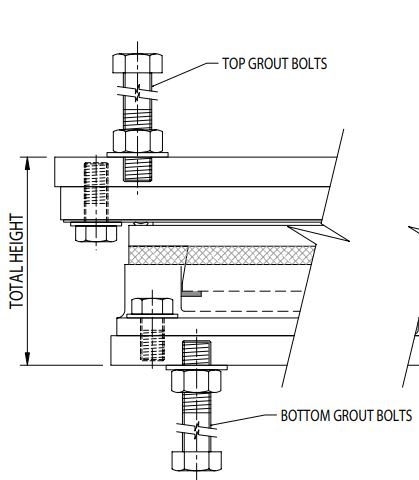
Does this change if we are considering Grade 4.6 (400 MPa / 58 ksi) or Grade 8.8 (830 MPa / 120 ksi) bolts?
Does it also change if the bolts are mainly in tension or shear?