canadiancastor
Structural
I have a light weight box structure meant to be hung on the exterior of a building on cantilevered channels. As it is outside of the building envelope, it would be exposed to rain, which is why I'm thinking of having it hot-dip galvanized. To keep things adjustable, I'm being asked to have horizontal slotted joints in both directions (for X and Z direction adjustability) with the use of filler material (for Y adjustability). I'm not sure whether this is reasonable or not because the loads are pretty low (in the order of 2 kips in shear and 2 kips in tension). I would be using slip critical connections, and calculating with AISC-360-16 J.3.8 leads to something around 4.8 kips for each 2 bolt connection (1 filler between connected parts, 1 plane needed to slip, Class A surface for hot-dip galvanized).
Second question, for the filler material, I'm being asked whether we could consider something like Koralath instead of galvanized steel plates. I don't see any issue with regards to durability, but I haven't found any information with regards to the coefficient of friction of Koralath. I also recall seeing somewhere that filler material needs to be non-compressible in slip-critical connections, I don't know if anyone has a more specific definition of "non-compressible".
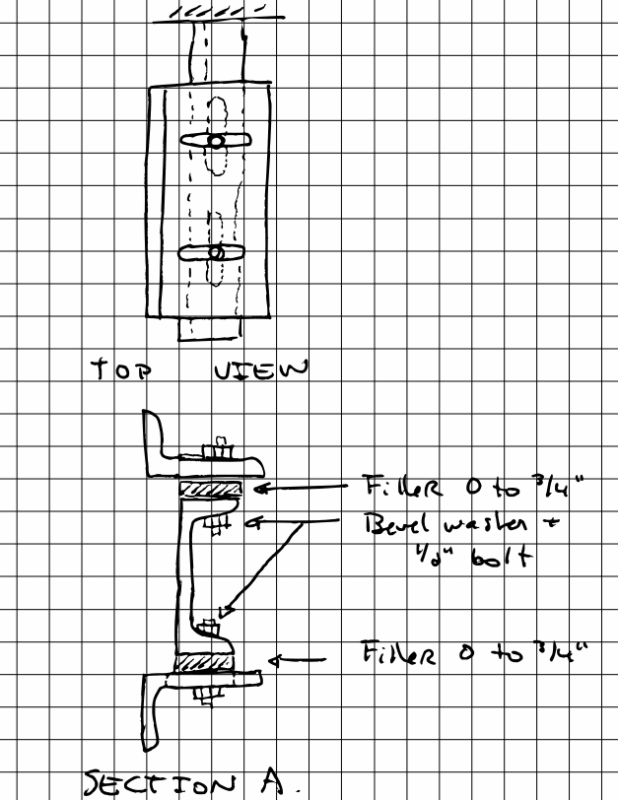
Second question, for the filler material, I'm being asked whether we could consider something like Koralath instead of galvanized steel plates. I don't see any issue with regards to durability, but I haven't found any information with regards to the coefficient of friction of Koralath. I also recall seeing somewhere that filler material needs to be non-compressible in slip-critical connections, I don't know if anyone has a more specific definition of "non-compressible".