oldisgold981
Mechanical
- Oct 16, 2021
- 17
Hello
I want to know when to use which kind of attachment.
Skirt can be attached(welded) to the vessel in the followings ways.
1. Skirt can be welded directly to the bottom of the head.
2. Skirt can be attached to the inside diameter of the shell, upto the tangent line.
3.Skirt can be attached to the outside diameter of the shell (id of the skirt is at the od of the vessel)
My question is,is there any guideline when to use which of the above attachment?.
What are factors that determine to use which configuration.
I want to know when to use which kind of attachment.
Skirt can be attached(welded) to the vessel in the followings ways.
1. Skirt can be welded directly to the bottom of the head.
2. Skirt can be attached to the inside diameter of the shell, upto the tangent line.
3.Skirt can be attached to the outside diameter of the shell (id of the skirt is at the od of the vessel)
My question is,is there any guideline when to use which of the above attachment?.
What are factors that determine to use which configuration.
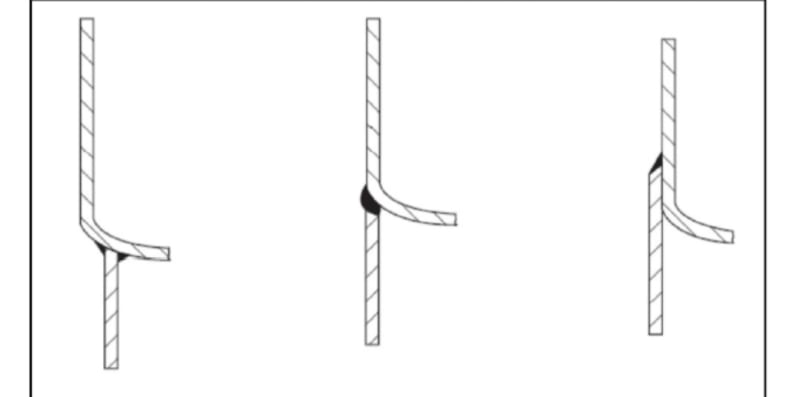