sticksandtriangles
Structural
I have a condition where due to a fabrication error, a very heavily loaded brace now has a 1" gap between the typical flange plate connection and the brace itself.
The contractor is asking us if a shim plate can be used to fill the 1" gap (see red shim plate) to prevent ripping it out and starting anew.
The load in the brace flange needs to flow into the shim plate and then transfer the load into the original brace flange plate. We have a very big 1" fillet weld connection in the original design on (3) sides of the plate. Does this red plate need to have any sort of strength? It feels like the load path is quite direct, in that the plate never goes into shear or tension and the load "flows" from one weld to another, with the plate just providing a welding surface to make the flow happen. Is there anything I should be checking on the shim plate?
Appreciate the feedback!
S&T -

The contractor is asking us if a shim plate can be used to fill the 1" gap (see red shim plate) to prevent ripping it out and starting anew.

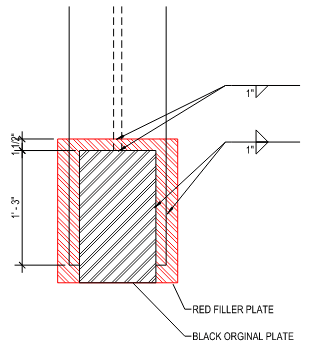
The load in the brace flange needs to flow into the shim plate and then transfer the load into the original brace flange plate. We have a very big 1" fillet weld connection in the original design on (3) sides of the plate. Does this red plate need to have any sort of strength? It feels like the load path is quite direct, in that the plate never goes into shear or tension and the load "flows" from one weld to another, with the plate just providing a welding surface to make the flow happen. Is there anything I should be checking on the shim plate?
Appreciate the feedback!
S&T -